Over the last few years there has been an increase in scaling observed in roadway and parking lot pavements in the Midwest. Several calls to the ASCC hotline, member photos, newspaper articles and issues noted by ready mixed producers and associations in multiple states are discussing this outcome. The purpose of this newsletter article is bringing awareness that several teams have started or will start parallel studies attempting to identify which factors are most likely contributing to pavement scaling and to invite participation by more ASCC contractors and ready mixed producer teams.
In an attempt to inform which issues are contributing to pavement scaling Hahn Ready Mixed stared a study in August of 2024 using 5 primary variables on (92), 2’x2’ test pads. The cost to set up a parallel study is only a few thousand dollars. The challenge is to have someone that will apply deicing chemicals and/or salts as often as the local roadways receive it during two winter seasons.
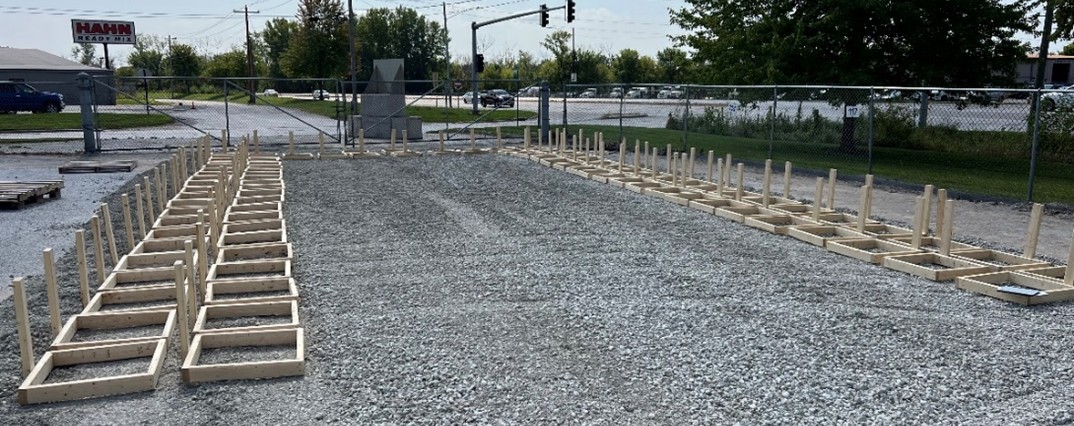
The Hahn Ready Mixed test pads will be exposed to freeze thaw conditions in Davenport Iowa with a combination of magnesium chloride prior to snow or freezing conditions, supplemented with rock salt each time the city applies them. After each winter season photos will be taken and reviewed by a panel of judges for deterioration, without revealing which variables are applicable to each photo.
The five variables being evaluated in the Hahn Ready Mixed study (link: https://hahnrmg-cdn.terrostar.dev/cms/wp-content/uploads/2024/11/Campaign_35.pdf) are:
- Slag – The slabs were all placed with either a IL (11) with 21% Class C fly ash replacement or a 65% IL(11), 21% slag, 14% Class C fly ash mix.
- Surface Vibration – half of the pads will be vibrated with a screed and the other half hand finished. In Davenport there has been a scaling correlation with parking lots placed with truss screeds or laser screeds. Unclear how intense the surface vibration was during the initial placements. Speculation is that either over vibration is affecting the near surface air entrainment or there is poor crew access to apply initial curing or intermediate curing chemicals due to the large area placed in a short period of time.
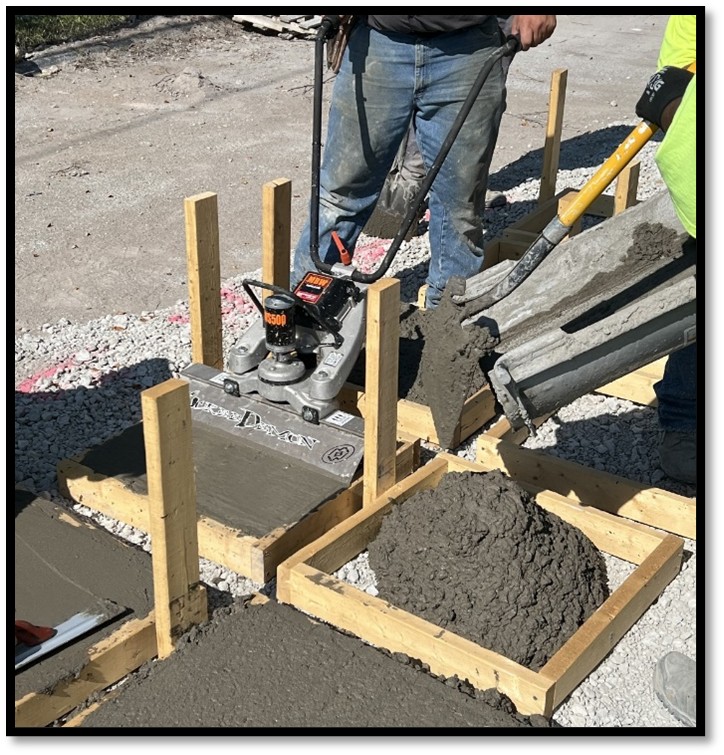
- Curing Compound: Some pads were not cured. Others received curing by either a wax based compound, PAMS (Poly-Alpha-Methyl-Styrene) curing compound, sodium silicate based cure or a solvent based cure and seal.
- Curing Timing – Among the test pads that received curing, half were applied 45 minutes after screeding and half 4 hours after screeding. The evaporation conditions on the day of placement were reported as ~0.15 lbs/sf/hr.
- Sealers – Sealers are often applied to protect against deicing chemicals and brines. In the study 1/3 had nothing applied, 1/3 received a silane/siloxane sealer 30 days after placement, a 1/3 received an admixture in the concrete which is intended to perform as an integral sealer.
All mixes used the same #67 limestone and natural sand. All pads were air entrained and had a polycarboxylate high range water reducer dosed at 2oz/100 lbs cementitious. They were placed over crushed limestone in late August conditions, starting at 85F and peaking at 93F with ~60% humidity and ~10 mph wind.
ASCC invited thirteen other state ready mixed association representatives, PCA, NRMCA and a handful of ASCC paving contractors to provide input on the Hahn study and possibly run a parallel study. The Tennessee Concrete Association, TCA, and ASCC contractor Stephens & Smith Construction (Nebraska) are planning to run a parallel study. Several other state ready mixed associations are discussing running studies with their local materials, potentially with other finishing techniques or curing methods.
Options already noted that could have been study variables:
- Evaporation retarders and finishing aids – ASCC member have reported an increase in the need for evaporation retarders or better, finishing aids. These are being used at rates lower than the traditional 0.20 lbs/sf/hr with IL cement and SCMs. Some parties are recommending applying these evaporation countermeasures as low as 0.05 lbs/sf/hr.
- Hydration Stabilizing Admixture – an option Hahn RM would have liked to try to see if a delayed set would cause surface crusting or plastic shrinkage cracking.
- Fresno Trowel – the use of a Fresno is controversial. Some people feel their use will close the surface too early. To me, like a lot of things, it depends on a diligent and experienced finisher to know when to use the correct tools, Fresno or other trowel.
- No SCM – In the 1/10/25 Teams call with 25 participants several people stated they wished one of the mixes would have been placed with either only I/II cement or only IL cement, whichever is locally available, to have slabs without SCM’s.
- Variable Weather Conditions or Late Season – There was discussion about placing in higher evaporation rate conditions or later in the construction season to shorten the time before deicing chemicals are applied. Both could put the slabs in a higher risk situation.
- Variable Water Cement Ratios – Many state DOT’s will have a water/cementitious ratio around 0.40 for slip form paving / low slump mixes. This is fine for mainline paving but very difficult to hand screed so parking lots can have a w/cm ratio of 0.45 to 0.48 which could allow snow or chemicals to penetrate into the concrete easier vs mixes with less water, depending on how they are finished and cured.
- Fly Ash or Natural Pozzolan – In some markets Class F is the only fly ash available. In other markets only Class C is available. Another option is natural pozzolans, made from crushed volcanic rock. Finally, some areas use ash blended into the cement as a IP or a IT with limestone and pozzolan.
The graph below from the American Coal Ash Association shows how much the availability of fly ash has declined due to coal fired power plants shutting down or switching to natural gas. From over 70 million tons per year 2002-2008 down to ~28 million tons per year in 2022:
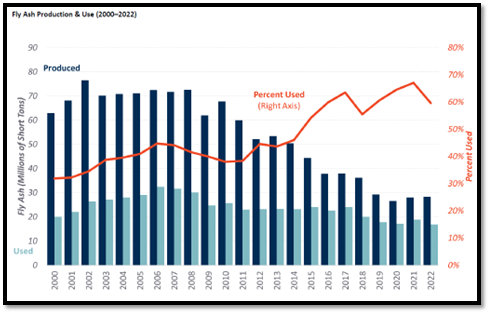
Natural pozzolans have filled some of the coal ash availably gap. They tend to have a higher water demand. Think of them as extremely small volcanic aggregates that need the moisture filled inside of them before additional moisture will be shared for hydration. It is similar to saturated surface dry (SSD) aggregate or sand.
All of these ashes, natural or man-made will react differently. This should be discussed with your ready mixed producer because each pozzolan will behave slightly differently in concrete set time influence, also depending on the admixtures and if it was introduced as blended cement or from a dedicated batch plant silo.
That is a summary of the scaling study in progress and some of the many variables that could be contributing to undesirable pavement outcomes. Please consider if the investment of a few thousand dollars and some time could help clarify which variables will help maintain a high quality, durable concrete pavement surface in your zip code.