Jim Klinger, Concrete Construction Specialist The Voice Newsletter May 2023
Question: We are building a post-tensioned (PT) concrete parking garage that features 3 levels below grade and 4 levels above street level. We bid the job to a General Contractor (GC) who in turn is working for a private developer. At bid time, the requirements for the quality of formwork and allowable deviations for formed concrete surfaces were stated in project specification section 03 11 00-1.04-B as follows:
1.04 Quality Control
A. General: Conform with ACI 301 except as modified by the requirements specified herein and the details on the Drawings.
B. Allowable Tolerance: Design, construct, set, and maintain the formwork so as to insure completed work within the suggested tolerance limits specified in ACI 347, Section 3.3.1.
C. See Section 03 35 00 for required traffic surface tolerances of slabs.
The "ACI 347" referenced above by the design team is ACI 347-04 Guide to Formwork for Concrete, which contains Table 3.1- Permitted abrupt or gradual irregularities in formed surfaces as measured within a 5 ft (1.5 m) length with a straightedge. The class of surface indicated in Table 3.1 is consistent with current ACI 117-10, section 4.8.3 Formed surface irregularities (gradual or abrupt).
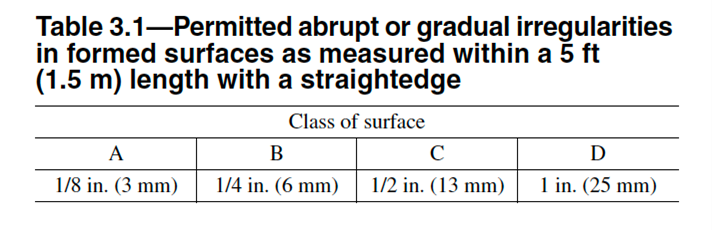
Prior to construction, we hired a professional formwork engineer to prepare formwork shop drawings that showed the shoring and reshoring sequences, concrete outlines, construction joints, large openings, and curbs. Cut sheets for the formwork materials (e.g. scaffold frames, aluminum beams, plywood, wall ties, form release) were submitted under separate cover. Our submittal was approved with only slight adjustments made to CJ locations by the engineer.
Formwork tolerances and form quality were not addressed on the shop drawings. The project preconstruction conference format (meetings traditionally held onsite in the construction trailer) was changed to a virtual meeting thanks to COVID. Much of that meeting was spent talking about COVID protocols and concrete ready-mix truck haul routes.
The topics of formwork quality and formed surface features never came up. The project is now complete, and we are having difficulties getting our retention payment. The GC (and Owner) are saying some of the columns we built do not meet the construction document requirements and need to be ground and patched. The photo of one of the garage columns indicates an abrupt surface irregularity (offset between adjacent pieces of column side formwork facing material) of one-half inch, maximum. Our position is that the as-built column depicted in the photograph meets all construction document quality requirements and that our retention should be released immediately. During the course of construction, no NCRs (noncompliance reports) were issued, and we are surprised to see this being raised now. Is the GC justified in holding our retention money?
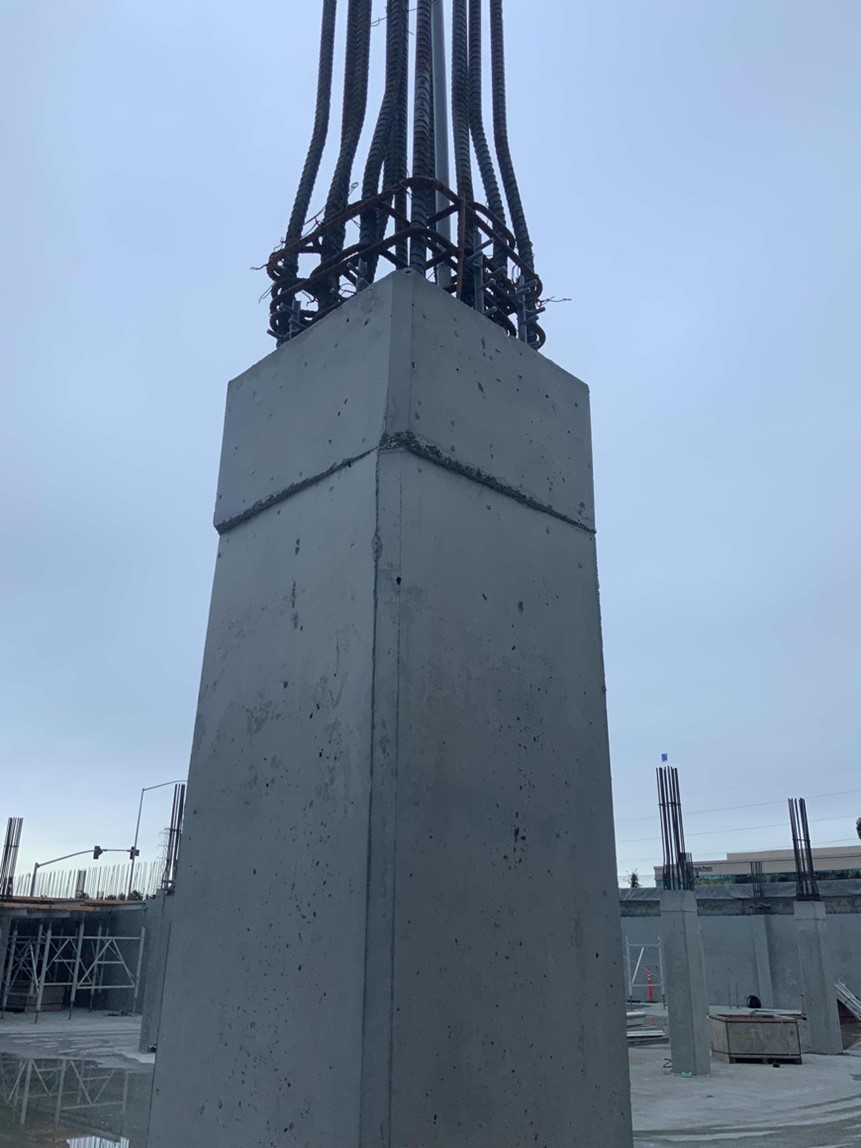
Answer: In a word...no. That is if the measured offset is indeed a half-inch or less anyway. Here's the story on this column and why it is plenty fine--contractually speaking--just the way you built it.
In theory, the design team is supposed to research and understand reinforced concrete, concrete tolerances, and the interface among concrete and all follow-on trades before confecting a fully coordinated set of construction documents. In a perfect world, said design team would have a working knowledge of ACI 117.1R-14: Guide for Tolerance Compatibility in Concrete Construction, which lays out the responsibilities of the various project stakeholders and suggests helpful strategies that can be used to keep tolerance conflicts and potential back charges at bay. In this case, the design team did not have a grip on the basics of concrete formwork tolerances right from the get-go, let alone trying to coordinate the work with any follow-on trades.
The problem started when the designers wrote specification section 1.04-B, above. Instead of doing the work and understanding the project, they punted and essentially said "just do whatever ACI says". The ACI class of formwork quality was never called out. Things got worse when the preconstruction meeting got derailed by COVID. Now it appears the Owner and GC are saying you somehow owe at least ACI Class B quality formed surfaces to the project.
There seems to be a fundamental misunderstanding of what ACI Class "B" is. Any competent designer knows that before putting pen to paper, the "Mandatory Requirements Checklist" in ACI 117-10 must be navigated. This is not an option, it is mandatory. The designer owes it to the Owner to complete the checklist before issuing the construction documents to bidders. In this case, had the designer read checklist section 4.8.3, it would be evident that ACI Class “B” is for "coarse-textured, concrete-formed surfaces intended to receive plaster, stucco, or wainscoting.” In other words, concrete covered later by the work of a follow-on trade. If the designer looked to see what Class "C" work is, it would become painfully obvious that Class “C” is the "general standard for permanently exposed surfaces where other finishes are not specified.” And this is exactly what you did. Since no other finishes are specified, Class “C” automatically kicks in by default. The half-inch offsets are OK. No uncompensated grinding or extra patching is required. You met your contract quality requirement and need to collect your retention.
(N.B.: I call Class "B" the "Blind Man's Tolerance.” There is nothing at all that is visual when you are dealing with Class B work. It's all about coarse textures and offsets and bugholes that can all be totally evaluated by touch. Class “B” has nothing at all to do with exposed concrete in a garage or anywhere else. You would be amazed at how many designers have not bothered to read, understand, and follow the ACI 117-10 Mandatory Requirements Checklist).
