Jim Klinger, Concrete Construction Specialist
The Voice Newsletter March 2025
Question: Two weeks ago, we kicked off the structural excavation, formwork erection, reinforcing steel placement, and concrete placement activities for the foundation supporting a 6-story post-tensioned (PT) parking garage located south of San Francisco airport (SFO). The garage is intended to provide 1540 parking spaces on a total floor area of 552,000 gross square feet. Suboptimal soil conditions (e.g. San Francisco "Bay Mud", typically found in the marginal coastland surrounding San Francisco Bay--the so-called "Bay Margin") documented in the project geotechnical report prompted the structural engineer to design a foundation consisting of driven prestressed concrete piles and a network of reinforced concrete pile caps and grade beams.
In similar fashion, the worst-case expected soils conditions caused the slab at grade level to be designed as a self-supported, elevated structural slab--10 inches thick-- with top and bottom layers of reinforcing steel.
(N.B.: The geotechnical report is unusually replete with warnings contained in a special, 4 page report supplement (aka "Appendix D") aimed at prospective bidders that describes the known risks associated with Bay Mud and the potential hazards that are likely to be encountered; not only by the mass earthwork contractors-- but by follow-on contractors as well--including shoring, foundation, waterproofing, utility, and even the landscape trades. The introduction to the appendix containing the guidelines appears as follows:
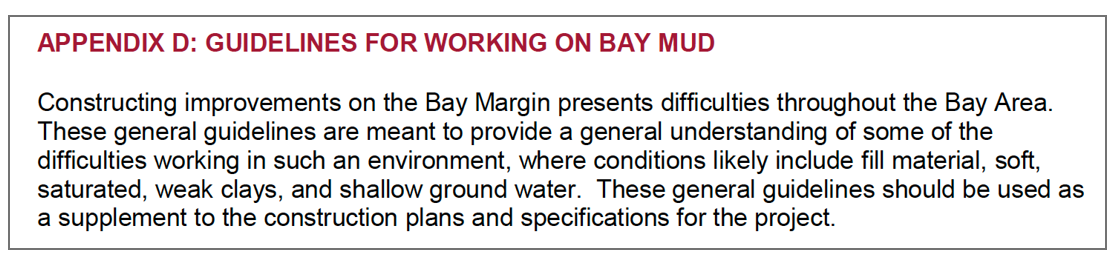
At the conclusion of the appendix, the following summary caveat to bidders and other stakeholders appears thusly:

In addition to the above, the Owner-Developer distributed similar "Instruction to Bidders" documents before bid time that advertised aggressive --but reasonably achievable-- schedule expectations.
One such bid instruction was a reminder to bidders that--even though the jobsite is more than a quarter mile west of any possible SFO flight path--each contractor is responsible for pulling a crane use permit from the Federal Aviation Administration (FAA). In our case, the top of boom elevation of our mobile crane will be a maximum of 120 feet above mean sea level. After conducting an aeronautical study, the FAA concluded that our equipment poses no "physical or electromagnetic effect to SFO aeronautical operations and procedures". Our crane does not even require any special marking or lighting.
Why is this significant? The FAA permit is a zero-dollar cost line item. But since the crane cannot be used until the permit has been pulled, the cost to the project in terms of time is the 3 to 4-week review turnaround time; a potential schedule delay (and potential fine) if this task is not handled in a timely manner. If the bid instructions had not warned of this requirement, our estimating and safety bid teams would have totally missed it.
In other words, no one among us could say that our bid teams weren't adequately warned of known potential risks before pricing and scheduling the work).
During the mandatory preconstruction conference held in the jobsite trailer, we were encouraged to meet with a design team that obviously were coordinated, had a firm grip on the project, and were motivated to collaborate with the contractors and suppliers. All stakeholders present agreed the level of detail provided for bidders presented in the geotechnical report and bid instructions was commendable, since it exceeds the "standard of care" usually found in such reports here in our local construction market. Unfortunately, not all of the project stakeholders seem to have gotten the memo.
Yesterday morning, we placed approximately 75 linear feet (LF) of foundation grade beams that support walls along the perimeter of the structure; walls that are on the project schedule critical path. This first lift of perimeter walls features tightly spaced reinforcing steel vertical bars (dowels), formed shear keys, and PVC waterstop along the bottom of the wall. Typically, such an interface at a construction joint among reinforcing steel dowels, keyways, and continuous waterstop presents conditions that require close attention to detail by our place and finish crew. There is little room for error, and plenty of opportunities for sloppy work to cause things to go sideways.
We placed the last "clean-up" load of concrete at 10:00 AM. At 3:00 PM, our labor crew began stripping the keyway boards, water-blasting the concrete spatter from the tightly spaced vertical dowels, and roughening the construction joint to the industry standard 1/4-inch amplitude specified in our construction documents. Our objective was to stay well ahead of the reinforcing steel crew-- standing ready in the staging area-- ready to start hoisting and setting the pre-tied reinforcing steel curtain panels. Once those steel panels are set, making any repairs or adjustments along the construction joint becomes difficult, expensive, and not schedule friendly.
So we were surprised to hear from the project inspector and the General Contractor (GC) that we are not allowed to water blast construction joints on the same day as concrete placement--essentially causing the GC to direct us to stop that activity. When challenged by our field superintendent, neither the inspector-- nor the GC-- were able to cite the chapter and verse we allegedly violated from the construction, ACI, or industry reference documents.
When we met with the GC and the inspector just before quitting time on pour day, no one was able to find any condition that featured loosened aggregate or dislodged waterstop along the freshly prepared construction joint. Neither the GC nor the inspector were convinced, but an agreement was made to follow up the next day.
Over the years, we have learned the hard way that it is best to avoid starting a range war with a difficult inspector, especially this early in the project. On the other hand, we don't want to have any part of setting a precedent that could haunt us for the remainder of the project. We are calling the Hotline to ask if ASCC has a Position Statement or knows of any information published by ACI or other industry source that discusses the minimum age of concrete before joint preparation can proceed; or that tells of a minimum time limit between placement of concrete in adjacent, abutting concrete pours. Please advise.
Answer: Great question. It seems like whenever we have a natural product with a relatively short shelf life such as concrete, timing is everything. In the concrete industry, for example, we have batch-to-placement time (BTP), which can put a maximum time limit on fresh concrete delivery. We have minimum wait times before steel can be erected--before certain forms and shoring can be stripped--and minimum recommended wait times before deicing salts and other chemicals can be applied to newly placed concrete flatwork.
Here at the ASCC Technical Division desk, we haven't seen much in existing industry literature per se that specifies or recommends a minimum time--expressed in days, hours, and/or minutes--that must elapse before construction joints can be roughened and prepared for the next, follow-on concrete placement. (More on this below).
As luck would have it, a similar question regarding maximum allowable time between placement of two elevated and abutting concrete slabs was fielded in the ACI "Concrete Q&A" column that appears in Concrete International magazine each month ("Allowable Time between Concrete Placements", ACI Concrete International, September 2012). In the response, ACI noted that exact timing is actually considered less important than the general age and condition of--and surface preparation of--the hardened concrete in the "first pour" before the concrete from the "second pour" is placed and vibrated. The following excerpt, based on ACI 224.3R Joints in Concrete Construction, appeared as follows:
"If only a few hours elapse between successive placements, a visual check is needed to be sure that loose particles, dirt, and laitance are removed. The new concrete will be adequately bonded to the hardened green concrete, provided that the new concrete is vibrated thoroughly...Older joints need additional surface preparation. Cleaning by an air-water jet or wire brooming can be done when the concrete is still soft enough that laitance can be removed, but hard enough to prevent aggregate from loosening".
According to the project superintendent, the intensity of the water blast was kept low; out of concern by your labor foreman that a strong blast might dislodge the embedded PVC waterstop--which confirms your crew met the spirit of ACI 224.3R. Unfortunately, a visual review of the construction joint "as built" made late in the afternoon on pour day was not enough to convince the GC and inspector that the work did not violate any of the construction document--or reference document--Quality requirements.
You should now be able to use the information presented above to gently educate the inspector--and the GC--that the work in place was prepared correctly, and the follow-on work can proceed.
Note: During our literature review to support this Hotline call, we did manage to turn up a reference in the ACI Collection that will be of interest to ASCC members who work on treatment plants, water tanks, and similar concrete structures. In ACI 350.4R-04 Design Considerations for Environmental Engineering Concrete Structures, section 5.2 offers the following design guidance: "At vertical construction joints, 48 h should be allowed between placement of adjacent wall sections".