Michael Hernandez, Technical Director
The Voice Newsletter February 2025
Its February, a polar vortex is dropping in and the local (Denver) forecast high temperature for 2 days from today is 14F. No placing exterior concrete in that. Most batch plants here shut down at 20F. Back in my operations days a few yards ago that sounds like a great day for either catching up on office paperwork, staff training or a field trip with a Superintendent and an office person. This winter I would encourage each team to schedule some field trips to visit a major material or equipment supplier, you will learn a lot about a supplier’s operation when you visit, and they are likely happy to show you, their facility. Meet some detailers, a batch man and other “behind the scenes” people that are critical to your success in 2025. See some formwork and equipment options. Bring some company SWAG like hard hat stickers or T-shirts. Those friendly gestures go a long way when you need a favor in the heat of the summer, crews are scattered, and placements are going 2-3/day. Some ideas:
Rebar Fabricator
This is one of my preferred field trips. The benders and shears might be silent on a bitter cold day, but if they are indoors, many are, it is a sight. Can see the logistics of how rail cars (ideally) or trailer loads of stock rebar come in, how overhead gantries bring bundles to a table and shake out the quantities needed. Then bars slide to shears and bend tables. Watching the auto bender take a spool of #4 bars and turn them into column horizontals or beam stirrups is mesmerizing. Do they run 1 shift? 2 shifts? Seasonal 2nd shift? Can understand their degree of automation, capacity, organization, cleanliness, quality control, safety culture and tagging system. All of those factors lead to complete orders and are necessary to know for large projects. Nothing worse than haggling right before the rebar inspection over whether a truckload that was supposed to have certain bars of a specific quantity had them or not then hot shotting the shortage. Visit a few fabricators and you will be able to internalize whose shop is most likely to get a big project done quickly and accurately.
May also see some rebar accessory options you had not thought about, like different chairs or couplers or terminators. There are many styles, all come with pros and cons as well as premium applications like architectural concrete.
Site logistics a challenge? Had projects where after a shop visit, we discussed with trucking operations how many trailers (1, 3...5?) they could leave on our jobsite and how they rig them so a crawler could plop one empty trailer on another to bring back to the fab shop after unloading them at our leisure. Helpful when the spring mud was deep to keep the rebar clean. The shop’s upside is the truck, and drivers are not sitting on standby waiting for a forklift or crane to unload them. Just detach the full load, hook up to an empty or stacked double empty and off they went.
PT Fab Shop
Post tension cable suppliers can be regional, hopefully there is a local one near you. Can see how the raw cable has their signature color of plastic applied to encapsulate the cable, cooled and spooled. Then the cables are cut to length, heads are pressed on, accessories applied and how the bundles are coded. Again, the size of the operation, from a handful of guys in a few hundred square feet to tens of thousands of sf to service a region. Talk with the detailers about pocket former options, ram calibration frequency and ideas about making your next project more constructable. Resolve issues like who is quantifying the carrier bar, detailing the busting bars (them or the EOR), are they seeing issues of how the bundles will be grouped or how the heads will fit at the face of a beam and column interface.
Formwork Yard
Winter is the time to see new alternatives in panels and shoring at a local formwork shop, particularly if you missed World of Concrete. Of course, WOC had everything. What you really need to know is what is locally available and what will need to be shipped in from elsewhere as soon as things get busy. Posts with tripods or shoring frames? Wall formwork pour rates? Can the guys lift the wall panels by hand or is equipment moving it all the time? Plywood options from MDO to HDO, plastic faced and their tradeoffs. Doka, Meva and Titan Formwork are Sustaining Members of ASCC. They all have a number of yards around the country, check them out.
Concrete Batch Plant
Ok, possibly not the most fascinating one on the list, but you need to know. How modern does the plant look? Central batched or dry batched? How many cementitious silos? Ideally 2+. How many aggregate bins can be loaded simultaneously, ideally 3-4, one is for sand. They often have a primary aggregate, like #57, that they use in most mixes, but some states will have unique blends. Inquire if the sand is natural or manufactured, you probably know this already, they will often have some optional aggregates or sands for a small premium. Manufactured sand often has a higher water demand. Ask about moisture monitoring of the sand stockpiles and how often this is checked. Understand whose cement and SCM’s they silo. They may have several cement suppliers to diversify their risk, or certain suppliers go to specific plants in the area. Ask if the trucks run in reverse after wash down to get all the water out of the drum or if they use a “rule of thumb” to estimate how much water is in the drum. Confirm the hold water will be printed on each ticket and watch the batching process a few times. The batch man does not often see outsiders so hopefully they are thrilled to show an interested person how a truck is loaded. See the integral color and admixture bulk storage equipment. There is more happening than you might expect. Then go to the backup plant nearby. Do they silo the same cement and SCM options? Better to know now than mid-slab placement that one silos I/II, another IL or IP cement.
Cement Manufacturing Plant
These are quite interesting beasts. At least I think so. At one end of the operation, blasting in a limestone quarry, at the other end trucks and rail cars being loaded with finished cement. Lots of crushing, milling, pre-heating, melting and grinding in between. I was most surprised by the number of quality control checks happening in each step of the process. It’s possible that the closest kiln may be in winter maintenance shutdown mode, if so, it will be easier to talk. If operating, they go 24/7 so be prepared for very large equipment, heat and some noise. The kiln monitoring room is watching a giant flame turn rocks into molten klinker and continuously monitoring numerous inputs and parameters, fun stuff. The finish mill is where the clinker, gypsum, limestone and possibly an SCM are ground and blended to make the final product, cement. Inquire if they focus on 1 main cement or have a diverse set of cements they make for masonry, oil wells (think high heat and pressure) or blends required by a DOT. They probably make more cement options than you had thought about. I might make a cement plant overview tour its own Voice article someday for a deeper dive on the steps in the cement making process and equipment like XRF, XRD and particle size analyzers to variety quality. Sustaining Member Cemex might be able to provide both a batch plant and a cement plant tour in the right city.
Caterpillar or Crane Yard
ASCC Sustaining Member Caterpillar has been an excellent host for the last few years so its easy to think about visiting them. Equipment advancements have been made the last few years that improve safety and productivity. Many dealers have a dirt stockpile out back that they let customers get a few minutes in the seat to feel how smooth the new model will operate. There will be more models and attachments than you can think of. Ask about the ASCC Member discount, which can be over $1000 on the right equipment.
Crane yard, similar principles. Maybe there is a 50 ton RT machine that is a nice fit between a 12k forklift and a medium crawler. Maybe an all-terrain truck crane that can roll in, pop up on outriggers and load a few truckloads to some back of project location, saving the crew from carrying it across a slab. Then there are the really big crawlers, my favorite. Be aware of ground bearing pressure and capacity, they are darn heavy. I have been partial to Manitowoc’s most of my career. 888 awesome. 2250 on a barge? Let’s go! The Manitowoc 16000 (440-ton capacity) is the only rig with the muscle within 500 miles to get that 55’ sandwich panel off the floor? It’s on!! When you just have to lift that 220,000 lb beam or panel, you have got to have fat stacks of steel on the counterweight tray. Options, we all like options.
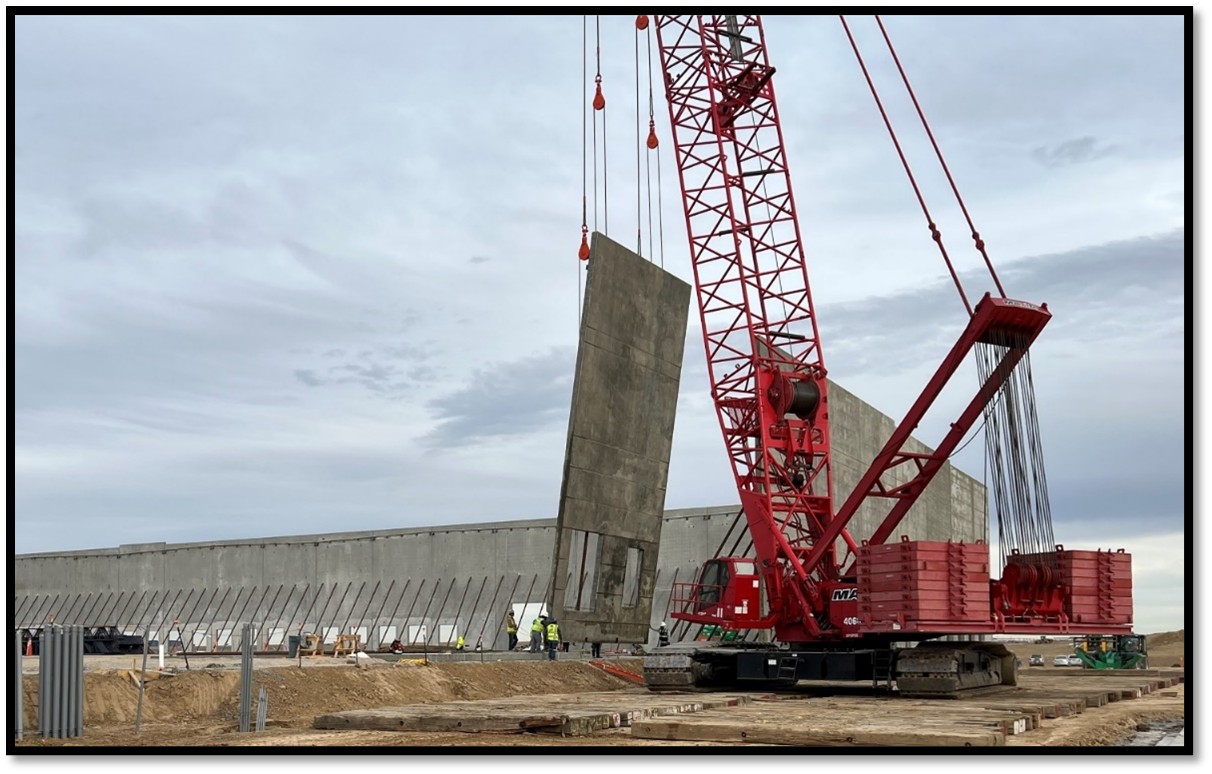
Manitowoc 16000 lifting tilt panels while on timber crane mats
Pump or Laser Screed Yard
Schwing and Putzmeister are both Sustaining Members of ASCC. ASCC members both buy from them directly or rent from a local pumper that buys from them. Big booms have big outrigger spreads. Use the opportunity to discuss pumping strategies. I do love a placing boom, probably the best option for placing slabs when higher than 5 floors. Dedicated stationary placing booms, SPB’s, rent by the month, detachable from a truck, by the hour. High-capacity trailer pumps are also a must in the mid-rise and high-rise market. This is nothing new if you are already doing this scope, but they keep evolving. 20+ years ago a 52-meter pump was BIG! Now a 65 meter on 7 or 8 axels can roll on site. This one might involve a trip to their U.S. corporate headquarters in Sturtevant, WI or St. Paul, MN. https://www.putzmeisteramericapresents.com/ or https://schwing.com/home.html These machines are a major investment so plan, plan and double check the plan.
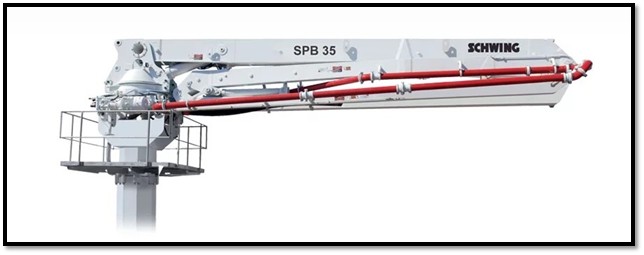
Schwing Separate Placing Boom 35m on pedestal mast
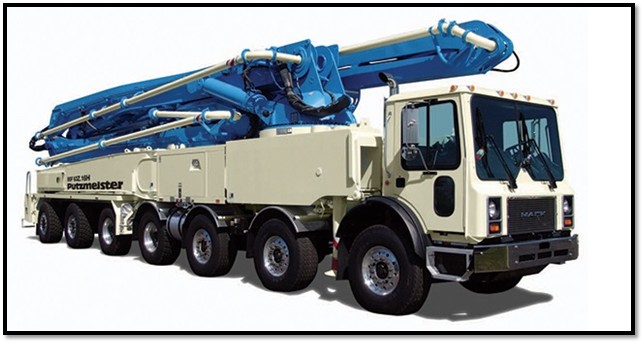
Putzmeister 63m Boom Pump with steerable rear axels
Somero is another ASCC Sustaining Member. The Sky Screed was my best discovery at 2025 WOC, even though it has been out for a few years. Can stand on a post tension deck and screed the slab with a smaller crew vs hand screeding and obtain higher F numbers. If the project tower crane has the capacity for a placing boom it can fly the Sky Screed too. Link: https://www.somero.com/products/stationary-screeds/sky-screed-36/
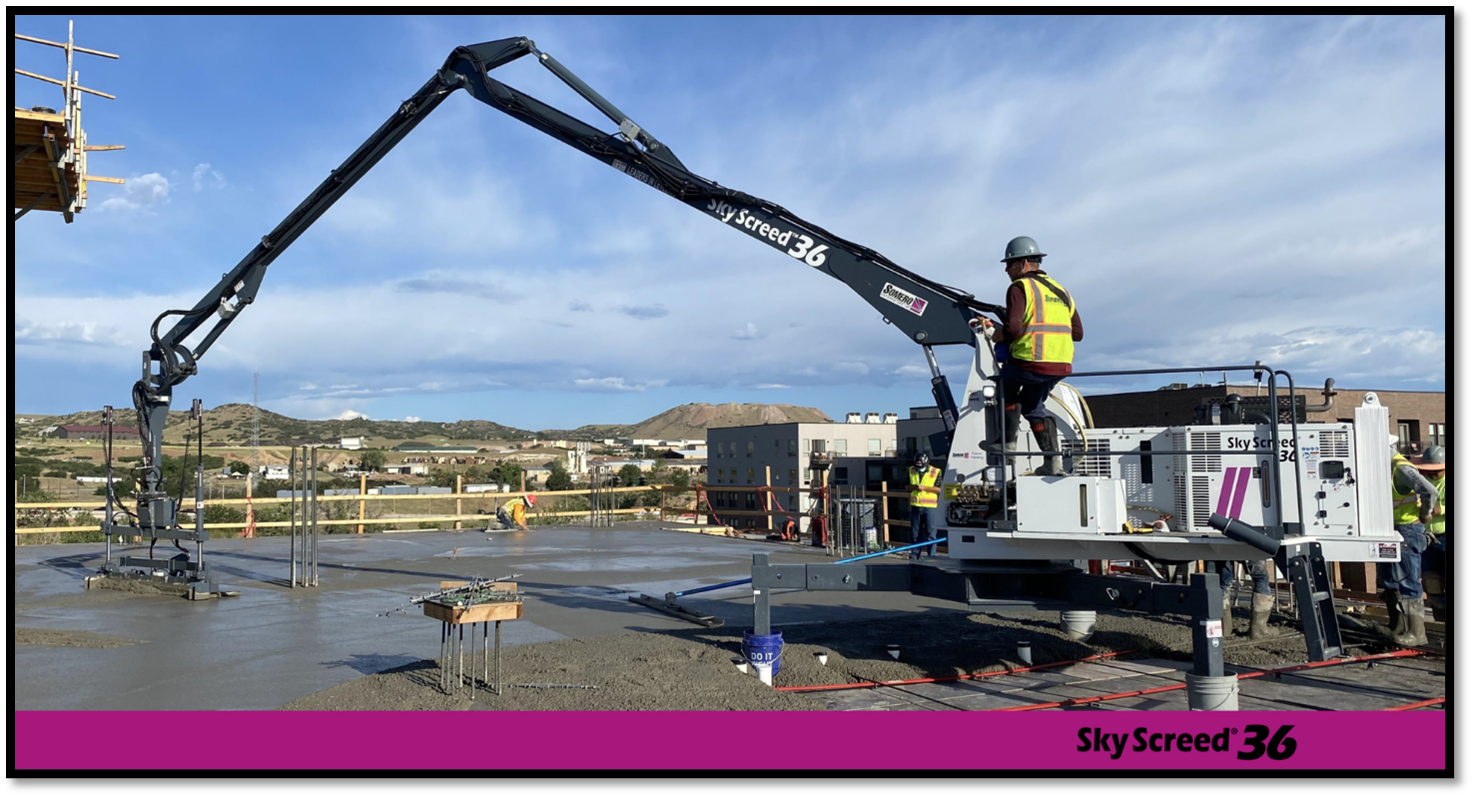
Somero Sky Screed with 36’ boom
In summary, don’t waste a winter non-pour day. Visit a shop, plant or yard. You will improve understanding and relationships. We all need an ally at times. Best to know who has the ability to come though when the need arises and what options they have in their toolbox.