Full disclosure: This column marks the 30th installment of the "Guidance for Concrete Contractors" educational series featured here in the pages of our ASCC VOICE monthly newsletter. What follows below is a modest retrospective, where we take a little stroll down memory lane--paved with concrete, of course--to see how the "Guidance" series has hopefully helped to keep us on time, under budget, and within ACI industry standard tolerances.
If you really want to know the truth about it all, out of all the Hotline calls that inspired the past 29 episodes, many serve as reminders that concrete construction is one tough business indeed--a high-stakes obstacle course-- peppered with daily hurdles for ASCC members to clear, and booby traps to be avoided (and hopefully outsmarted) at every turn.
Construction booby traps are typically known to go off at any time between bid day and final retention payment. In the worst cases, we might even blaze right past the scheduled contract end date and wind up yet another year later sitting in some attorney's office for deposition with our final payment amount hanging in the balance.
Over the course of that "Guidance" 29-column run, we encountered all kinds of creative backcharge issues--some amusing, some even offbeat--ranging from misunderstanding of what constitutes ACI 117 class B formwork offset tolerances to the time allowable for rainwater in a birdbath to evaporate. We found out why certain slag concrete wall surfaces may appear greenish-blue when form panels are stripped. And, for ASCC concrete estimators, we suggested carve-out qualification language for contract bid proposals to help neutralize potential risk items--and protect your margins.
We constantly encouraged "Guidance" readers to always try to have a look inside the other guy's playbook in order to defend ourselves from questionable backcharges. In doing that, we discovered why the concrete guy is not responsible for cleaning up shot-on shear stud ferrule debris prior to metal deck fill placements--and why it is the metal building contractor that owes the shims under the metal building wall stud sill tracks--and not the concrete contractor. And we learned that breaking out the project manual and spending just a few hours before bid time leafing through the odd-numbered project specifications (usually just between divisions 1 and 9 is all it takes) to see what scope the follow-on trades owe the project--a practice which can often prove to be a very wise--and profitable--time investment.
And, of course, we had to get a grip on the unfortunate reality that some of these booby traps are self-inflicted--and totally avoidable. Sometimes, the problem is your basic, brand-X field error: the crew put something in the wrong place in the heat of battle. At other times, it was disclosed during several Hotline calls that the crews installing the concrete work had never read their project's Division 3 specifications governing their scope; had never seen their own subcontract "Exhibit B"; and had never even been exposed to industry standards ACI 301 and ACI 117. These are among the most important documents that govern almost every project concrete scope. They must be carefully read--and fully understood-- especially by all onsite personnel immediately responsible for performing the work. There used to be a time when contractors were required to perform this simple task by keeping a collection of all relevant ACI reference documents within reach in the jobsite trailer, as you can see in section 1.3.3 below, excerpted from this 2005 version of ACI 301:
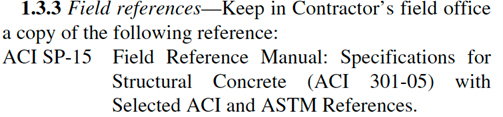
Insider's note: Evidently, this jobsite reference document requirement has been scrubbed from the specification and does not appear in subsequent versions of ACI 301. As of today, however, this essential reference compilation itself has been updated, renamed, and reissued as publication "MNL-15(20) Field Reference Manual: ACI 301-20 Specifications for Concrete Construction With Selected ACI References". No matter what one's job title happens to be (e.g. Superintendent, Estimator, Inspector, Project Engineer, and so on) MNL-15(20) can prove to be one of the most valuable document investments an ASCC member can ever make over the course of one's entire career in concrete construction.)
By and by, we explored potential strategies and methods (March 2021 VOICE article: "Blindsided by COVID-19") to recover costs when ASCC contractors were blindsided by COVID-19. Right behind COVID, the Hotline started receiving calls alerting us to another issue that was catching concrete contractors (and other stakeholders) by surprise: the roll out of Type IL cement, aka "portland limestone cement or PLC". Since then, the controversies surrounding limestone cement have grown as use of PLC increases market share replacing I/II or II/V cement in more and more urban and rural construction markets.
Although there were a few concrete engineering consultants located in our midwest and southern markets who had already been privately commissioned to investigate reported potential side effects of this new blended cement, we here at the Hotline didn't actually start fielding PLC Hotline calls placed by ASCC members until summer of 2022. By that time, the World of Concrete producers were already well-aware of the PLC issues being reported in certain US markets. To stay abreast of these breaking industry developments, World of Concrete 360 (WOC360) organized two PLC-related seminars scheduled to be held at the Las Vegas event in January 2023. This Hotline Operator attended both of them.
The first of the WOC seminars we attended was presented to a large, completely packed room by former cement industry insider Tim Cost, P.E., FACI called "What You Need to Know About the New Type IL Portland-Limestone Cement". We found the Cost presentation to be informative, straight-up and fair--coming from an experienced engineer and researcher who had spent many years himself employed by one of the major (e.g. worldwide conglomerate) cement industry players. Included in the Cost presentation were acknowledgements of reported PLC , side effects especially in several areas of vital importance to ASCC concrete finishers: bleeding, water demand, possible surface crusting, set time and obtaining acceptable finishes on high-FF/FL (e.g. trowel finish) floors. Based on the content and quality of the presentation, Cost was invited by ASCC to speak at the ASCC CELF 2023 event. Three self-explanatory slides that summarize the content and the recommendations from the Cost WOC and ASCC presentations are shown below:
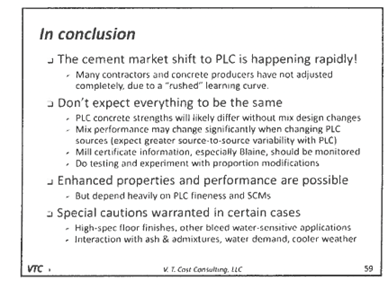
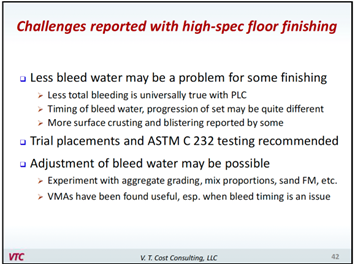

The second 2023 WOC presentation attended by the Hotline was sponsored jointly by WOC360 and ASCC, called "Quality in Concrete Slabs Luncheon and Forum: Preventing Problems with Slabs on Ground--Preconstruction Considerations When the Project Calls for a "Green" Floor".
Moderated by concrete consulting firm Structural Services, Inc. (SSI), the panel included a petrographic analysis expert (Meredith Strow/Twining), a concrete contractor (ASCC member David Venegas/Vemac), and a cement industry technical sales engineer (Stephanie Hampton/Heidelberg Materials).
Although this event was billed as a generic discussion of so-called "green" concrete slabs, the presentation quickly turned to a discussion of Type IL cement. This was indeed the hot topic of the event, and the panelists had obviously become very familiar with potential PLC side effects long before the Hotline became aware of them.
Anyone who attended that 2023 WOC event can tell you straightaway about the question and follow-up comment this Hotline Operator posed to the panelists:
"Some ASCC member contractors are losing money in both overtime and rework because this "new" material does not always perform as advertised. This change from ordinary portland cement to Type IL cement is not the concrete contractor's idea. It is not our change. Who is going to reimburse the concrete contractors for the money we are losing in rework and overtime?"
And the follow-up, memorialized by ASCC member Jason Wimberly on the social media platform LinkedIn:
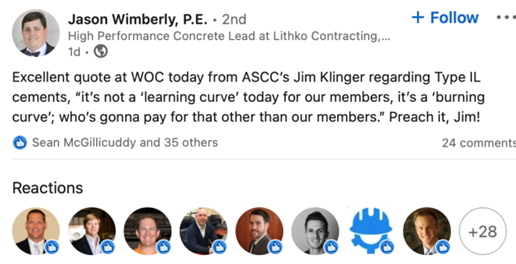
Shortly after the 2023 WOC event in January, the Hotline posted a PLC Frequently-Asked-Questions (FAQ) column in "Guidance #14" (Feb 2023 VOICE and the results of the ASCC member-only PLC survey conducted between Dec 2022 and Feb 2023 in "Guidance #15" (March 2023 VOICE). Both of those are available for members to read in the ASCC web page archives.
Now here we are, some 15 months later after the publication of "Guidance #15". Much water has gone under the bridge since then related to Type IL cement.
A fair amount of progress has been made, thanks to collaboration among ASCC members (and some non-members) from all across the concrete industry who have pitched in and generously donated their time, insights, and work product.
But there is still work to do before we can get this one behind us and prepare ourselves for the next wave of alternative materials that the experts are telling us is on the near horizon (if not in use already). Part of that work includes collaborating with ready mixed and cement trade associations, encouraging adjustments to industry advertising campaigns and product messaging, which can lag behind the variety of customer field experiences as documented in several industry surveys, industry publications, events, seminars, and so on.
The ASCC Hotline, for example, is still fielding calls from contractors--several here over the past few months--that report a recent epidemic of scaling problems across the midwest and upper midwest construction markets. One publication that comes to us from the hallowed halls of academia explains the unusual 2023 epidemic--and its three root causes--as follows:
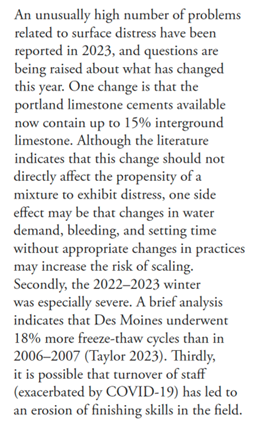
Hotline Translation:
Root cause #1: It is the concrete contractor's fault for not changing our long-standing, and customary finishing practices to handle PLC side effects in "the literature" e.g. changes in water demand, bleeding and setting time.
Root cause #2: It was the weather's fault.
Root cause #3: It was COVID-19's fault. During the pandemic, the academics claim, we lost our good finishers and were forced to hire unskilled replacements. Therefore, scaling is really the concrete contractor's fault for hiring substandard finishers. See Root Cause #1, above, or--better yet-- check out Gene Hackman and Keanu Reeves in "The Replacements".
Once we move past the pedantic silliness of the above academic root cause dissertation, the scaling problems in the real concrete construction world are so bad for a few midwest states that some Owners are reportedly floating the idea of abandoning concrete as the paving material of choice and reverting back to asphalt concrete (AC) as the sole-source material option. Obviously, these are not the kind of discussions we want prospective Owners to consider, let alone even having Owner or other stakeholder exposure to such talk as is currently being featured in newspaper articles, social media platforms, and even the excerpt from academia quoted above.
Well, there you have it--a modest look back at the past 29 episodes of the ASCC VOICE "Guidance" column. What will the next 30 episodes bring to ASCC VOICE readers? Stay tuned...we'll have to use the "trowel and error" method to rinse that one out.
In the meantime, what follows below is the Hotline assessment of topics likely to be found listed in many current industry committee meeting agendas and event programs: finishability problems with commercial trowel finished concrete floor slabs, and how we must all collaborate together during the introduction of additional blended cements or SCM’s like ground glass into the concrete construction marketplace.
___________________________________________________________________
Big Thanks to the American Concrete Institute
Anyone can see plain as day that the two most pressing topics facing the concrete construction industry today are related to Sustainability and the continued side effects of PLC. Viewed through a big-picture lens at 40,000 feet, it is also fair to say that the prime mover and facilitator in assisting ASCC--and the industry at large--to both collaborate and make progress with Sustainability and PLC challenges is the American Concrete Institute (ACI).
(Insider's note: When it comes to ranking these issues in order of importance, it appears by far and away that Sustainability and PLC are the top two issues of concern to ASCC members (see estimate, below). The third topic, of course, is Constructability/Productivity. We will focus on Constructability and Productivity in more detail in future installments of the ASCC VOICE "Guidance" series.)
Over the past 15 months, ACI has given a tremendous amount of encouragement and support, enabling ASCC to collaborate with ACI on the following Sustainability and PLC-related work products:
-3 recent articles in Concrete International (Dec 2023, Jan 2024, Feb 2024);
-The ACI Foundation sponsored the ACI 302-ASCC I/II to IL Slab Mix Study
- Budgeted time for PLC discussions in ACI Committee meetings;
-Hosting Special Sessions at ACI Conventions (see below);
-Conducting a joint ACI-ASCC industry-wide PLC survey;
-Hosting webinars and on-demand presentations through ACI University and
-ACI participation in ASCC Sustainability (and other) Committee meetings.
To put this all in perspective, we can try to estimate the impacts related to Sustainability and PLC on the concrete industry at large by examining the schedules of Special Sessions sponsored by ACI at Convention events. We simply count them--and observe the trends. The table below is an approximate workup showing the past 8 ACI Convention events and the number of Sustainability and PLC Special Sessions offered at each. Note that there was a string of ACI Conventions that were cancelled as in-person events and held virtually (e.g. Oct 2020 Raleigh, N.C., Mar 2021 Baltimore, Md., and Oct 2021 Atlanta, Ga.).
As can be seen in the table below, over a span of 8 ACI Conventions there were 29 Sustainability sessions and 16 PLC sessions. If we keep in mind that there were multiple speakers who presented at some of the sessions--sometimes perhaps 5--that is an indicator of the large amount of diverse information and resources that ACI provides for the concrete industry at Convention events and a fairly good indicator of the industry importance of both Sustainability and PLC issues.
Based on the flavor of recent Hotline calls regarding PLC and the progress made by ACI and ASCC on the Sustainability front, it appears the upward trend in ACI Special Sessions offered at future Conventions may continue.
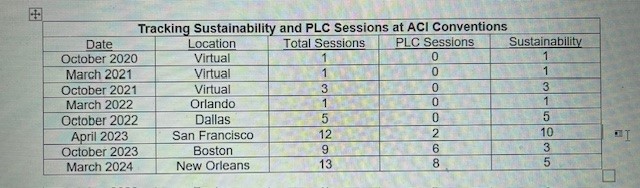
The forgotten trowel finish slabs: part 1
All concrete industry stakeholders need to be operating with the contractor's awareness of our ultimate collective objective--which is Owner satisfaction with the latest acquisition of a brand-new, custom-made, reinforced concrete commercial facility with a trowel finish floor as its centerpiece. In other words, it is entirely fair to say that during the so-called "roll-out" of PLC, not enough attention was paid to research, testing, and consulting concrete contractors for guidance concerning one of the most important bread-and-butter work products that many of our fellow ASCC concrete finishers routinely produce on a daily basis: high-spec, trowel finish concrete floor slabs.
(N.B.: the phrase "collective objective" recognizes the easily and oft-forgotten fact that--as a collective group, all of us--architects, engineers, cement producers, ready mix producers, material suppliers, and ASCC concrete contractors-- all are ultimately working in service to...and at the pleasure of...the most important stakeholders of all: the Owners.)
According to results of our recent joint ACI-ASCC PLC survey presented in the February 2024 issue of Concrete International, some 80 percent of Owners say concrete slab problems are occurring at a greater frequency with PLC than with OPC (ordinary portland cement). Many ASCC concrete contractors are currently contending with frustrated Owners who have high Quality demands--and expectations to be compensated if those demands are not met. Indeed, for industrial distribution facilities, trowel-finished concrete floor slabs are not just the appearance centerpiece, but also serve as the durable working surface the Owners count on to generate revenue. Any short-term or long-term concrete Quality issues that affect the Owner's ability to make money are certain to add to the concrete contractor's exposure as well.
At a recent industry event, ASCC Vice President and Board Member Anthony DeCarlo reminded us of the perils of future roll-out miscues as follows:
"The problem is that nobody seems to be looking at Type IL cement from a finishability standpoint. They don't realize the end-user Owners are actually looking at our trowel finish concrete floors as the showpieces of their new facilities. If we are producing concrete that can't be finished by traditional methods or finished to the level the Owners are expecting, then our industry as a whole is going to get a black eye".
To put this in perspective for those who have never set foot on an active jobsite, DeCarlo brings his expertise as the CEO of a concrete contracting company to bear by defining what the term "traditional methods" means to an ASCC concrete contractor tasked with managing the finishing crews responsible for producing trowel-finished concrete floors required to meet very demanding Owner expectations:
"It takes about 3 to 5 years to train a good concrete finisher. But if the cements keep changing--and the way these cements react during a slab placement keeps changing--how can anyone expect these finishers to be able to read the floor and decide what tools and machines need to go where...and when? All the variability we are experiencing with Type IL is making it more difficult to train new finishers, makes experienced finishers concerned about their skills to produce an acceptable finish, and continues to increase the risk contractors bear."
___________________________________________________________________
Jewels in the Crown: Slab Owners...and their Consultants
As ASCC contractors have reported, the most common PLC side effects occur when the contracted work products comprise trowel-finished concrete industrial floor slabs. As Anthony DeCarlo and other contractor CEO's will tell you, the trowel finished concrete floor slab is considered by many Owners to be the "Jewel in the Crown" of their new commercial facility.
So for ASCC concrete finishers, the pressure is on. In today's construction environment, the current breed of Owners is not interested in flawed floors, they want perfection. To get a view through the lens of a concrete floor slab expert, we talked with long-time ASCC member Scott Tarr, PE, FACI, President of North S. Tarr Concrete Consulting, based out of Dover, NH.
Scott Tarr is not a concrete contractor himself, but his work is well-known among the ranks of ASCC contractors. Tarr co-authored the ASCC publication "Guide to the Design and Construction of Concrete Toppings for Buildings" with partners Ron Kozikowski and Matt Sheehan, and has recently produced a webinar for ASCC that covers "Slab on Grade Design Options". As a Fellow, Tarr's accomplishments at ACI range from author of articles, session presenter, and many years' worth of ACI Committee work. Tarr is also a forensic engineer, expert witness, and a Constructability consultant.
To address the topic at hand, we asked Tarr to explain his role as Constructability consultant to several national, high-profile commercial building Owners. As an expert in the design and construction of high-spec, trowel finished concrete floor slabs, Tarr often has his hands full dealing with constant Owner expectation management, starting from initial meetings during the Owner's conceptual phase all the way through to project completion.
Tarr explains it this way: "It's a consultant's job to inform the Owner of what they reasonably should expect based on industry standards, the slab design itself, selection of concrete contractor, time of year, and so on."
And what are these very competitive, high-profile Owners telling consultants like Tarr?
One such Owner heads up a nationally recognized capital investment firm-- a successful group of investors at the top of the real estate food chain who lend cash to high-end developers in a highly competitive business arena. Before consulting on the schematic architectural design portion of a new company headquarters building, Tarr was given the following criteria by the Owner: "This will be our flagship headquarters building, and we expect the concrete floors to look like they're in a museum--so our customers know we pay close attention to details when they visit us".
In another concrete floor consulting case, the company president brought Tarr in near the end of the design phase to review plans for one of the company's typical big-box, tilt-up shell structures--nothing fancy or spectacular--until you got inside to the concrete floor. During a meeting with the Owner, the design philosophy was explained to Tarr thusly: "We realize that the construction documents do not specify the project itself to be "Architectural Concrete" per se, but at the end of the day, in order for us to be able to sell the building, it will come down to a beauty contest between our concrete floors and those of our competitors in our regional industrial real estate market".
The third example cited by Tarr has some interesting twists. The Owner in this case is a group of capital investors who specialize in all aspects of the co-called “big box” commercial facility business – design, build, buy, sell, renovate, flip. In other words, these folks are simply in the business of buying and selling commercial real estate. In what might be called astute gunsmanship, these investors themselves have become quite expert at performing their own in-house concrete slab condition surveys and using visible features to estimate future maintenance costs based on observable crack fields in concrete floor slabs. If, for example, their in-house survey indicates just a few cracks, the building can command a higher price, since future maintenance costs could be projected to be minimal. For this Owner, industrial concrete floors with crack fields become bargaining chips to be used in sales negotiations. In one example, even though Tarr provided a report discussing the cause and proper repair of cracks, the capital investors used the visibility of the cracks (albeit repaired) to submit a $500,000 counteroffer, discounted from the listed selling price based on their in-house research and condition survey of the existing slabs in that market. For this reason, excessive visible random cracking has become a sensitive issue for Owners.
“As a consultant”, Tarr says, “I am obligated to advise my clients that any expectations of perfect, crack-free floors (or any cost analysis that does not include future floor maintenance costs) are not realistic and are not consistent with the preface that appears on the cover page of ACI 302.1R-15 Guide to Floor and Slab Construction. I tell Owners that concrete contractors will always strive for perfect, defect-free floors, but perfection cannot be guaranteed with a natural product such as concrete.”
Reasonable expectations should be established, and effort should be made to minimize the number of visible defects. Several industry guides, including ACI 302.1R section 5.2.9.3 and "Concrete Floors on Ground" published by the Portland Cement Association (PCA) include the following statement:
"Some random cracking should always be expected, even with sufficiently close joint spacing. It is reasonable to expect random visible cracks to occur in 0 to 3 percent of the surface area floor slab panels formed by saw-cutting, construction joints, or a combination of both."
According to Tarr, “this expectation for a conventionally-jointed floor was developed to suggest to Owners that zero cracks is not realistic but also that cracking in more than 3% of the slab panels can be excessive. While some feel 3% isn’t enough, we have found that cracking in less than 1% is common and 3% is a generous allowance. In any case, for any random cracks, we recommend considering the location, length/width, and cause of each crack to determine its expected performance in order to develop an appropriate remedy.”
___________________________________________________________________
The forgotten trowel finish slabs: part 2
Since its formation in August 2023, the work of the ASCC PLC Task Group has had immediate, worthwhile benefits for ASCC concrete contractors and concrete industry stakeholders at large. Although the proceedings of the Task Group meetings largely remain unpublished, it is fair to report a consensus has been reached concerning two key points. The first point is acknowledgement of the fact that the industry message of "1 to 1 replacement with no side effects" has been effectively debunked. The second point is recognition that the PLC product was brought to market before the often-reported side effects on trowel finished slabs (e.g. changes in set time, bleed rate, water demand, finishability, and so on) were fully understood by the material producers and communicated to concrete contractors and other stakeholders.
In other words, introduction and increased use of the "new" material have come with some unintended consequences. Industry event organizers have recognized this is currently a hot-button topic which has generated totally packed rooms at World of Concrete, ACI Conventions, and in-person ASCC events. Recent example: Anyone who attended any of the PLC-themed Special Sessions at recent ACI Conventions could see straightaway that the venue's rooms were not adequate to accommodate the standing-room-only crowds gathered there to learn about and discuss one of the more difficult questions posed to the concrete industry at large in recent memory: "How can material suppliers introduce alternate cements into the marketplace and avoid unintended consequences at the same time?"
(N.B.: During one of the ACI Special Sessions offered at the recent ACI Convention in New Orleans titled "From the Lab to the Field--Experiences with Portland Limestone Cement, Part 1 of 2", the PLC conundrum was put into perspective by ASCC member Jason Wimberly, PE, FACI during a "Question and Answer" exchange with session moderator Stephanie Hampton. What follows below is a condensed, paraphrased account of that exchange. For VOICE readers who are interested in listening to this Special Session in its entirety and in context (highly recommended by the Hotline), a recording was made by ACI and is--at present--available to ACI members who attended the New Orleans Convention on the YouTube platform via the ACI "On Demand" service).
Toward the end of this ACI Special Session, Wimberly asked the panel group this question regarding R&D, pre-release mockup testing of PLC trowel finished slabs:
"...How much side-by-side, full-scale testing...was done by the cement industry in partnership with readymix producers and concrete contractors...and does the cement industry, noting all the problems that have been very verbally addressed, have the intention of doing that (full-scale testing) when they begin to drop even new further supplemented cements onto the marketplace...?"
The response was fielded by moderator Hampton--quite candidly, too--as paraphrased thusly: "...unfortunately, to my knowledge, definitely not in the Mid-Atlantic area...I think that was an oversight...I 'm just going to apologize to everyone on behalf of the cement industry. It's one of those problems that--obviously--we want to try to work together, all playing in the same sandbox, but unfortunately, on my behalf, I can say in my area it (testing) was not done. Do I think such testing needs to be done? Most certainly. Do I think that's the best way to probably mitigate future situations? Most certainly."
____________________________________________________
ACI Past-Presidents: Checklists to the Rescue
Based on what we all know today, it is fair to say that--as an industry--we cannot afford to repeat the "growing pains" associated with the previous development and roll-out of an alternative material. Everyone agrees the process of bringing future alternate materials to market can--and must--be improved. But how--and by whom?
Thanks to examples set by ASCC, ACI, NRMCA, and other industry collaborators, we believe we are now well on the way to assembling the components and framework needed to help solve a very complex set of problems.
One resource we can leverage for guidance is the work product of ACI past Presidents. For example, when it comes to defining the ACI Core Values of "Camaraderie, Consensus, and Credibility", we look to the landmark column by ACI past President James Jirsa, who was the first ever to discuss how to "play nice in the sandbox"--ACI Committee style. Jirsa's October 2000 treatise describes something many of us have witnessed in person at ACI Committee meetings--rip-roaring fireworks coming from both sides of the aisle during contentious technical arguments. But--at the end of the day--consensus is reached, and no one drives home mad.
If the problem set to be solved features issues of efficiency in reinforced concrete design and construction, we can consult with structural engineer and ACI past President Cary Kopczynski, or--even closer to home--ACI past President Mike Schneider, for guidance in matters of Constructability and Productivity. Schneider is an ASCC Founding Member, and is reportedly one of the few concrete contractors elected President in ACI history. Schneider is also known for stating in a Constructability presentation "I've never seen email drive a single nail or place a yard of concrete".
When considering the complexities of the comprehensive testing and vetting process required to appropriately develop and introduce new alternate materials into the concrete construction marketplace, we can make good use of the vast experience and published work product prepared by yet two more ACI past Presidents and ACI Honorary Members: Terry Holland and Ken Hover. Their piece of the puzzle? A so-called "product data sheet". But viewed through the lens of ASCC concrete contractors, we see it as a thorough and sensible checklist--similar to the many ASCC checklists developed over the years in conjunction with the NRMCA and other concrete industry partners.
Originally assembled by Holland and Hover to ensure appropriate material vetting, the suggested 64-item checklist appeared in their August 2020 ACI Concrete International article titled "Proposed Data Sheet for Alternative Cementitious Materials". Aimed by the authors at an intended audience of prospective material suppliers, the checklist is designed to make sure all relevant project stakeholders are consulted before a new material can be brought to market. Simply put, concrete producers, architects, engineers, and most important--concrete contractors--must be included in the conversation in order to be considered for use in a project. Presented in generic fashion, the proposed checklist "incorporates questions based on more than 100 years of experience with concrete materials, including the SCM's (supplementary cementitious materials) that are in common use today".
A portion of that "100 years of experience" cited above includes the efforts behind the introduction of silica fume into the marketplace during the 1990's. At that point in his career, Holland was involved in those efforts from the silica fume proponent side of the aisle. "Engineers kept asking us for data to support our proposals that silica fume material be incorporated into their structural designs", Holland recently explained to the Hotline, "If we had a checklist like this back then, obtaining acceptance would have been a whole lot easier to introduce the new silica fume product to the marketplace."
Although the article is aimed at potential material suppliers, the authors tell us that the checklist will provide information of interest to Owners and building officials as well: "The Owner must be made aware of the use of the proposed material and of the risks and benefits the material presents. The building official must be comfortable that the material will perform as intended and provide the appropriate level of life safety for the project".
The proposed ACI checklist itself is drawn straight out of the classic "Constructability" playbook, which--by industry consensus definition--stresses early involvement by project stakeholders as the course of action recommended to greatly improve the chances of project success. As described above, the alternate material checklist itself contains 64 line items, distributed over 7 separate categories: General, Concrete Production, Contractor Considerations, Structural Considerations, Durability Considerations, Sustainability Considerations, and Considerations for the Architect. Of those 7 categories, the sections that concern ASCC concrete contractors (Part C) and architects (Part G) are excerpted below:
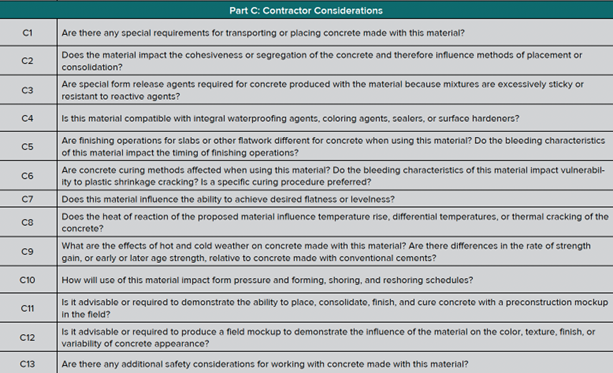
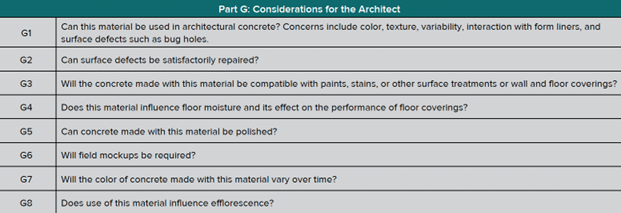
It seems sensible that the ASCC and our other industry partners could incorporate the Holland and Hover checklist into our playbook, which already includes Alert! #1, Alert! #2, the ASCC-NRMCA Preconstruction Conference checklist, and if it is a performance-only specification, then the ASCC-NRMCA P2P checklist. Considering all 5 documents together, then, all the right boxes could be checked--and all the right questions could be asked--to provide the best chances of success when the next alternate cementitious material comes rolling down the chute.
The forgotten trowel finish slabs: part 3
Many of the accounts concerning the potential PLC side effects experienced with trowel finished concrete floor slabs (e.g. set time, bleed water, water demand, and finishability) have been disclosed during ASCC Hotline calls without benefit of photograph--or video--documentation. Largely driven by NDA (non-disclosure agreement) restrictions, many of us are forced to rely on verbal or written descriptions to help us visualize how the reported side effect symptoms would actually appear in the field. Until now, that is. Thanks to several ASCC contractor members, a few video clips have been generously made available for inclusion in this 30th Anniversary edition of the VOICE "Guidance" column.
The first video clip comes from long-time ASCC contractor member Steve Lloyd, FACI. In this 17-second video clip, the concrete finisher is seen checking surface crusting by using finger pressure when slab cracks appeared while the floor slab was still being trowel finished. This indicates the slab is setting up from the top, down--the opposite of what concrete finishers have been trained to recognize and have typically experienced with OPC over many years of trowel finishing concrete. Here's a Dropbox link to the Lloyd video described above:
https://www.dropbox.com/scl/fi/q0bt6tzzau93twj9aksf9/Stevie-Lloyd-clip-1.mp4?rlkey=dl1t1fsjtzg0sxpg45w0ntnse&st=xsy0mtcl&dl=0
The next 2 video clips come from long-time ASCC contractor member Joe Neuber, FACI. Both clips were filmed during the mockup test placements #2 and #3 that were presented in the January 2024 article in ACI Concrete International; co-authored by Neuber and titled "Minimizing the Risk for Portland-Limestone Cement Concrete Slabs". In the video clip filmed for mockup #2, a finisher is seen checking surface crusting using finger pressure, similar to the Lloyd example, above. In the video clip taken during mockup test pour #3, severe cracking and surface crusting is evident. Dropbox links to the Neuber mockup test video clips described above are here:
https://www.dropbox.com/scl/fi/x3zzheb6ao7cz82soicmg/Neuber-test-pour-2.MP4?rlkey=e9a05y3px7thax5obx8ox7mb1&st=8c5jkieg&dl=0
https://www.dropbox.com/scl/fi/yhwyhk7d4isga2s5jbm3a/Neuber-test-pour-3.mp4?rlkey=24gy9r10t6f1lhzw0rer6xqrq&st=4c1su9a1&dl=0
The final video clip comes to us from an ASCC Hotline caller, filmed during a placement of PLC concrete intended to receive a follow-on dry-shake treatment as part of the finishing process. Even though the clip is a mere 8 seconds long, that is really all that is needed to demonstrate what some PLC forensic experts call the "apple pie crust" side effect, another indicator of a concrete slab setting from the top, down.
(N.B.: Perhaps unknowingly giving away their age, other long-time concrete finishing experts have told the Hotline this 8-second clip is graphic evidence that showcases the "waterbed" effect.)
The Dropbox link to the classic PLC "waterbed" video clip is here:
https://www.dropbox.com/scl/fi/iw2hric0m754sdfw4pm3e/Hotline-PLC-waterbed.mp4?rlkey=htll6eq62xzj9z8qvwg0xw4v7&st=8gysix8x&dl=0
(Insider's note: Of course, not every trowel-finished concrete floor slab that features PLC in the mix is going to exhibit such finishability challenges as those documented above. But the next time you hear an experienced ASCC concrete contractor speak of problems with water demand, or lack of bleed water, or "apple pie" surface crusting...at least now you will be able to visualize straightaway the side effects the concrete finisher is describing.)