Jim Klinger, Concrete Construction Specialist
The Voice Newsletter May 2024
Question: We are estimating a mid-rise, pump-place-finish only job (P-P-F) that bids roughly 2 months from now. The base building structure is framed in steel, featuring seismic frame columns founded on a network of pile caps and connecting grade beams. The slab on grade (SOG) has a footprint of 44,585 square feet (SF). The SOMD total trowel finish quantity is 254,926 SF on 6 floors, including the roof. We figured we would assume 12 each pumped concrete placements of 350 cubic yards (CY) each on floor slab areas averaging 21,000 SF each. The total SOMD quantity of 3000 psi normal weight concrete (NWC) is estimated at 4208 CY.
This is a private, mixed-use medical research facility with flatness and levelness "F-numbers" specified at most slabs, including elevated slabs on metal deck (flatness only at SOMD). According to the Instruction to Bidders (ITB), the building has been fully leased and so the tenants are known, but the end uses of each floor space are still unsettled. One example that was floated to all bidders was a slab on grade envisioned as a large kitchen with tiled floor, servicing an employee cafeteria space with an exposed polished concrete look. On the other hand, the ground floor might be used as office space, with a cubicle farm that supports laboratories on the floors above. In other words, all stakeholders know going in that the final tenant improvement (TI) scope is a moving target. We have been directed to bid an assumed baseline of F-numbers, with Owner acknowledgment that there are likely to be additive change orders once the TI scope finally gets locked in.
If you really want to know the truth about it all, we are not thrilled with either the project Ownership or the general contractor (GC). This is based on previous unsavory experiences involving back-charge disputes and collecting retention in a fair and timely manner. But times being what they are, we made the business decision to bite the bullet and quote the work anyway.
On the last job, we worked with this same owner and GC, disputes arose with a follow-on flooring subcontractor who couldn't get a grip on the concept that the as-built top elevation of finished concrete slab surfaces can potentially--and normally--change with time. Thanks to ASCC Position Statement #6 (and a mind-numbing number of job site meetings), we were finally able to spit the hook and avoid back charges after the Owner agreed to cover any flooring contractor substrate adjustment costs.
Truth be told--part of the difficulties we experienced can be attributed to our own project team having a limited grip on the quality and tolerance requirements that govern our finishing scope--let alone the contents of the contract itself. From a business standpoint, such an internal breakdown in communication and lack of situational awareness is both unacceptable and unsustainable.
After that project closed out, we dropped back and did what we should have done in the first place, which is to read and fully comprehend the project contract floor finishing specifications themselves and the relevant industry documents from which they were drawn (e.g. ACI 117-10 Tolerances, ACI 302.1R-15 Guide to Concrete Floor and Slab Construction, and so on). Thanks to 20-20 hindsight, we now appreciate the value of the required preconstruction tolerance coordination meeting(s) specified in the mandatory language in ACI 117-10 section 1.1.3 as follows:
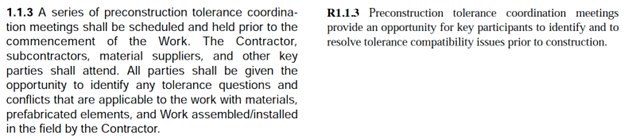
So now here we are, preparing to bid on an entirely new project. We want to make sure that that between our written bid proposal qualification letter and the mandatory preconstruction tolerance coordination meeting described above that all stakeholders--including our field personnel-- understand how and why the finished concrete slab surfaces are likely to behave throughout the project (and beyond)--and who bears the burden of paying for any "no-fault" substrate adjustments as outlined by ASCC in Position Statement #6.
In. other words, we are clear now on how to handle "no-fault" substrate adjustments based on the guidance in ASCC Position Statement #6. But what are the protocols when "no-fault" becomes "yes-fault" (e.g. when our finishing crew fails to meet the required F-numbers)?
During our in-house, retroactive due diligence exercise, we noticed in the Dipstick Operator's Manual prepared by the FACE company a sample random traffic floor flatness/levelness specification that presents several options to remedy out-of-tolerance finish work: remove and replace, grinding, and skim coating. We also noticed a fourth option, which involves giving the Owner a credit to compensate for non-complying work as described here:
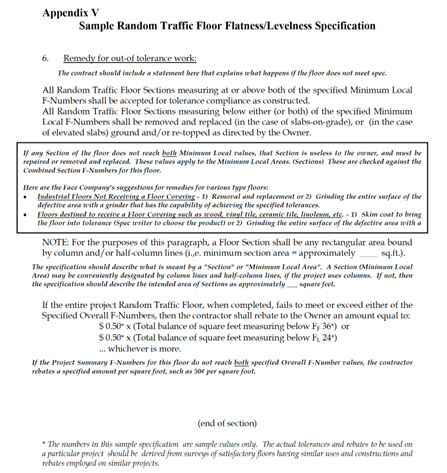
What can the Hotline tell us about option #4--the rebate?
Answer: ASCC Position Statement #6 is one of the most used--therefore one of the most valuable--documents in the ASCC Hotline technical library. This document is the result of a successful collaboration effort conducted among ASCC and many of the follow-on flooring trades with whom costly back-charge disputes typically arise. The message contained in Position Statement #6 is that the apparent trade "incompatibility" is actually a "no-fault" phenomenon to the extent that neither concrete contractors nor follow-on flooring contractors are able to control the technical reasons for the inevitable changes in concrete floor top surface contours over time e.g. curling and slab deflection. After the draft document was prepared and floated to the follow-on trade representatives for review, the end result was their endorsement and permission to use their brand logos on our Position Statement cover sheet as shown below:
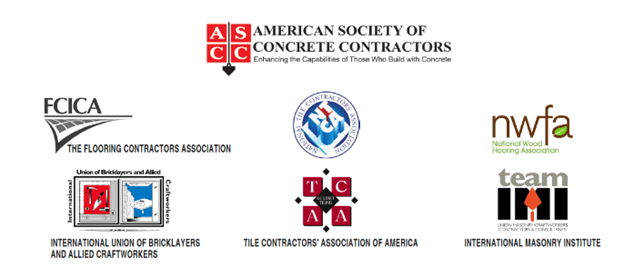
Taken as a stand-alone document, ASCC members have been able to convince GC's and Owners at various stages of a project (from pre-bid RFI's to unfortunate disputes many months after a slab has been placed and finished) that the right thing to do is for the Owner to fund potential slab surface adjustments via an allowance line item carried in the Owner's budget.
Sometimes, however, the background that drives Position Statement #6 may need to be submitted upstream to Owners, GC's and designers--along with the document itself--for educational purposes. Fair enough request.
The best document we have found that presents the complete back story and technical rationale that supports Position Statement #6 and is aimed at all concrete construction stakeholders can be found at the Construction Specifier by using this link.
Written by ASCC Hotline operators emeritus Ward Malisch and Bruce Suprenant, the article titled "Bridging the Specification Gap between Divisions 03 and 09: Concrete and Floorcovering Associations Unite" takes the reader on a step-by-step, easy-to-understand tour described by the authors as follows:
"Division 03 specifies concrete floor surface flatness requirements to be installed by the concrete contractor. Division 09 specifies the concrete floor surface flatness for the flooring installer that must be met before installing the floorcovering. What does it mean when these requirements are incompatible?"
"The Owner does not want a specification battle; he or she just needs a concrete slab that allows the floorcovering to be installed to achieve a good appearance and obtain the manufacturer's warranty. Clearly, there must be a cost-effective and efficient solution. Cooperation among the American Society of Concrete Contractors (ASCC) and six associations has led to a solution for bridging the specification gap between Divisions 03 and 09."
We recommend this article be attached to every copy of ASCC Position Statement #6 that our members send upstream--for whatever reason.
So the above takes care of everything you want to know about the "no-fault" scenario. But what about the "yes-fault" situation, particularly the "rebate" method of making the Owner whole when the concrete finish work is non-compliant?
Crediting money back to the Owner via deductive change orders (or retention adjustment) as a remedy for non-conforming work is nothing new. But here at the Hotline, we have only heard of a few cases where the concrete contractor has admitted to such a commercial arrangement for not meeting the floor tolerance requirements. Usually, we hear about the first 3 options e.g. remove and replace, grind, or skimcoat.
We do know that the rebate option is mentioned twice in ACI 117-10 Specification for Tolerances for Concrete Construction and Materials. This option--albeit called "liquidated damages" in the Commentary--appears in sections R4.8.4 and R4.8.5.2 as follows below:
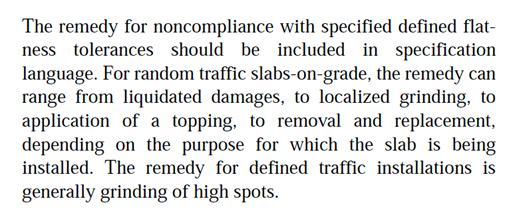
Commentary section R4.8.4
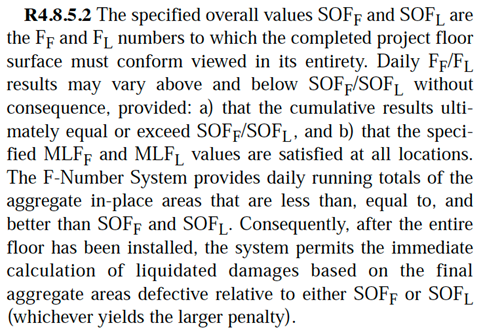
In addition to the rebate example suggested in the FACE sample specification described above, we found an example of a similar rebate scenario in a 1996 article by Eldon Tipping titled "Using the F-Number System to manage Floor Installations" as shown below:
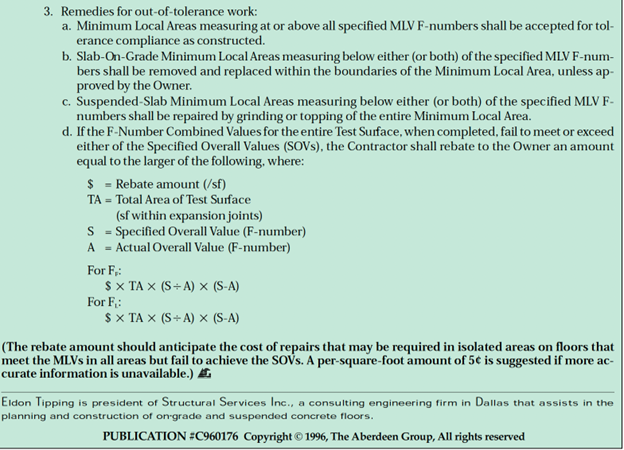
The key to either way of calculating "rebate" or "liquidated damages" dollars is making sure the agreement is in writing before the work starts and that the credit unit rate passes your in-house reasonableness test.
The FACE example suggests a credit unit of 50 cents per SF. The Tipping example suggests a credit unit of 5 cents per square foot.
Depending on the floor section size and your local market cost of place-and-finish labor you carry in your estimates, both numbers could make sense when weighed against the cost of a potential, unknown back-charge at some time out in the future.
(N.B: neither the FACE nor the Tipping examples show us an example calculation-- and description of any backup--that one presumes would have to be submitted to an Owner for review before a rebate arrangement could be inked. If you are viewing this through the lens of the Owner, what would you need to see before you agreed to a unit rate intended to make acceptance of substandard work product palatable?)
__________________________________________________________________
Input Needed--Rubbed Finishes Update
Over the past 50 years, there has been much confusion about what constitutes a rubbed finish and how such a finish is mocked up, reviewed, and eventually accepted by the customer. In addition, concrete curing specifications requiring forms to be left in place for 3 to 7 days--and a trend toward stronger concrete mixtures--have made rubbing so-called "green" concrete difficult to near impossible. We want to illustrate ASCC contractor concerns with rubbed finishes with a focus on specifications, costs, and durability.
(N.B.: The term "green" in this context refers to early-age, freshly hardened concrete, say between 24 to 48 hours after placement.)
The goal here is to prepare an article regarding rubbed finish "best practices" with a possible Position Statement to follow. To make that happen, we need input from concrete contractors. In January 2020, we asked VOICE readers to send us their experiences with rubbed finishes. Unfortunately, all of us were sidetracked by more pressing issues. Now things are starting to settle down a bit, and we want to focus on back-burner items. Here's some background and an update:
Examples of Rubbed Finish--Past and Present
1970: A project specification called for a rubbed finish applied with a silicon carbide (aka "carborundum") brick on an exposed concrete wall for a county jail in Illinois. The nominal specified wall concrete strength was 3000 psi at 28 days, and the forms were removed the day after placement. At that time, fins were removed and the wall was rubbed, creating enough paste from the green concrete to cover bugholes and fin removal lines.
2015: A project specification required a rubbed finish on the soffit of an elevated post-tensioned (PT) concrete parking deck in Houston, Texas. The specified PT slab concrete strength was 5000 psi at 28 days (nominal), with a requirement for high-early strength of 3500 psi at 3 days to allow PT to be stressed. On day 4, the concrete in place was too strong to receive a rubbed finish. As a result, fins and offsets were addressed with a hand-held grinder, and bugholes had to be filled with additional grout before the surface was sacked.
The compressive strength of the "green" concrete when rubbed in 1970 was probably on the order of 500 psi, while the concrete rubbed in 2015 was (in theory) at least 3500 psi. There is clearly a significant difference in procedures and cost in rubbing 500 psi concrete and trying to rub (and probably hand-grinding) 3500 psi material. We need to convey these differences and impacts to designers, specifiers, and other industry stakeholders.
ACI 301 Specifications
After conducting a literature survey of relevant industry documents, we found rubbed finishes have been specified in ACI 301 Specifications for Concrete Construction since 1960 in various forms-- including "smooth rubbed finish.” "sand floated finish.” "grout cleaned finish,” and "cork floated finish.” The 1972 specification discontinued the sand-floated finish. The 1996 specification added that a smooth, rubbed finish was to be accomplished after the period required for curing by leaving the forms in place. Early versions of the specification stated that a smooth rubbed finish was to be produced on "green" or "freshly hardened" concrete.
The 2005 version of ACI 301 stated "...produce finish on hardened concrete no later than the day following formwork removal...Use no cement grout other than cement paste drawn from the concrete itself by the rubbing process.” This creates a conflict with specifications requiring form removal at 3 to 7 days since the concrete will be too hard to draw paste from the surface. The rub finish then escalates to grinding the fins and offsets and adding grout and then sacking. This rub to a grind/sack scenario creates a changed condition that is rarely recognized and paid for. Thus the concrete contractor gets left holding the sack and absorbing the cost.
Now jump forward another 15 years to 2020...The latest version--ACI 301-20--specifies rubbed finish as follows:
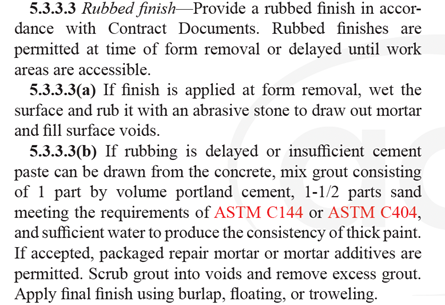
In our opinion, section 5.3.3.3 should be adjusted to make it consistent with other sections of the ACI 301 document that require specifiers to clearly designate the scope of work in Contract Documents. The operative words here are "designate" or "designated"--terms used some 50 times throughout the ACI 301-20 version.
(Example: in ACI 301-20 section 6.1.1, the requirement for the architectural concrete scope is specified as follows: "This section covers construction requirements for concrete designated as architectural concrete in Contract Documents.”)
We suggest the following suggested revisions be brought to the attention of ACI Committee 301 for consideration:
In section 5.3.3.3, revise to read "Provide a rubbed finish in the areas designated in the Contract Documents".
We also suggest this revision also be incorporated into the Mandatory Requirements Checklist section 5.3.3.3 as follows: "Designate portions of the Work to receive a rubbed finish".
Based on the above (and as discussed in the latest ASCC Technical Committee meeting), we are looking for feedback from contractor members as follows:
What are your experiences with rubbing concrete surfaces?
Can you send us examples of bizarre or conflicting specifications?
Can you provide relative cost information on any rubbing work or rework?
How was rubbing handled if it was not specified in your specs?
What are your best practices for rubbing concrete?
Please send your feedback via email to jklinger@ascconline.org