Jim Klinger, Concrete Construction Specialist The Voice Newsletter March 2024
"I heard it...I heard it...I heard it on the X..."
______________________________________________________________________________
Full Disclosure (back story):
Every so often, the ASCC Hotline receives calls for assistance regarding concrete that is resistant to elevated temperatures (aka "refractory" concrete), but these inquiries have generally been limited to domestic fireplace and pizza oven-type terrestrial applications. Upon further review, there may be ASCC VOICE readers that might wish to know more about the extreme--and exotic--uses of such refractory concrete. For those curious members...you are in for a treat.
__________________________________________________________________
During the initial test launch of the "Starship" vehicle from its SpaceX home base in Boca Chica, Texas, a good chunk of the reinforced concrete launch pad infrastructure--referred to by SpaceX as "Stage 0"--was blown to smithereens by the exhaust plume generated by its stage 1 cluster of 33 "Raptor2" rocket engines capable of kicking out some 16 million total pounds of thrust. Slabs, grade beams, drilled piers--the whole 9 yards--were pulverized, as depicted in the photo below.
One "Business Insider" headline reported " Starship's first liftoff toward space created the equivalent of a volcanic eruption in the launchpad, physicist finds".
The Los Angeles Times reported the initial test launch of the world's most powerful rocket "blasted concrete up to 6.5 miles away".
When you watch video footage that documents the April 20 2023 launch (use link to one such video, below), pay attention to the large chunks of debris splashing into the nearby Gulf waters--way out past the third breaker--on the right side of your screen.
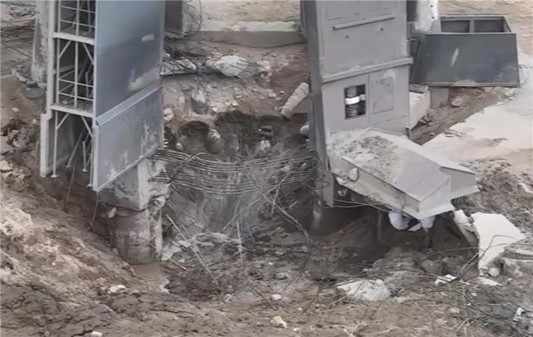
"Stage 0" launch platform at Boca Chica. Photo credit: the platform called "X".
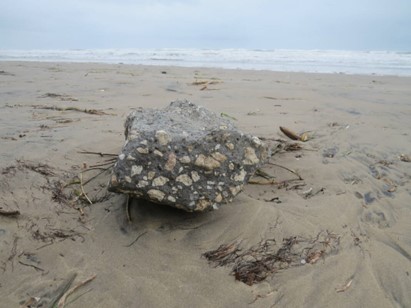
Photo credit: Steve Clark/ Brownsville Herald (Texas).
At T-plus 4:04 minutes after the last of the Starship stack cleared the tower, the trajectory of the launch vehicle veered off course, requiring a destruct command to be given to abort the mission. The Federal Aviation Administration (FAA) declared the event a "mishap", and stated "the Starship broke up, resulting in the loss of the launch vehicle."
But a Tweet posted by SpaceX just after the "mishap" romanced it another way:
"As if the flight test was not exciting enough, Starship experienced a rapid unscheduled disassembly before stage separation". (N.B. SpaceX considered the initial test to be a resounding success, since all they really wanted to do is get the super-heavy rocket stack to clear the tower. The voice of Mission Control said at the time that anything after that "was icing on the cake.")
The FAA immediately grounded SpaceX, since the launch license was valid for one launch only. In order for the FAA to issue future launch licenses, SpaceX themselves conducted the mishap investigation and submitted it to the FAA for review, complete with an itemization of some 63 proposed corrective actions that SpaceX would guarantee to implement before another launch would be licensed.
Although we could not find the SpaceX mishap report in the public domain, we do know that several infrastructure corrective actions proposed by SpaceX included "redesign of the launch pad to increase its robustness."
So the obvious question then becomes: "What were the root causes of the failure of the concrete portion of the "Stage 0" launch pad infrastructure?"
It is public knowledge that a special proprietary refractory concrete ("Fondag") was used by SpaceX-- a concrete mixture featuring synthetic aggregates and calcium aluminate cement--that reportedly performed just fine during a static mockup test firing done at roughly half of the Raptor engine cluster's max power. We also know from Tweet traffic posted the day after the mishap that SpaceX proceeded with its test launch despite missing a key Stage 0 component--a steel, water-cooled blast diverter plate--as described by the founder of SpaceX below:
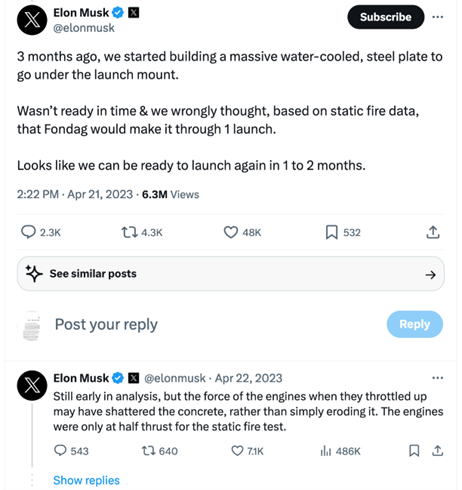
We may not ever see a complete account; since we were not able to access the SpaceX/FAA mishap report, and Elon Musk has yet to return inquiries from yours truly requesting a copy. We have also been unable to find the identity of the concrete contractor--and the ready mix supplier--who worked on the Stage 0 infrastructure.
At the time of this writing, SpaceX has obviously satisfied the FAA's requirement to prove the proposed corrective action punch list was implemented, since two subsequent Starship test launches have been made from the Boca Chica facility--the most recent on 14 March 2024--without any reported damage to the reinforced refractory concrete portion of the "Stage 0" structural frame.
There are several contemporary video accounts describing launch pad refractory concrete that can be found via simple internet search. Perhaps the best of the lot was produced after the November launch. Titled "What Exactly Happened to Starship, Did Stage Zero Actually Survive the Launch?", this interesting account and analysis can be accessed with this link.
Another sensational video that showcases earlier SpaceX experiences with obliterated (and glowing) launch pad refractory concrete--along with an excellent treatise on refractory concrete in general--can be found in the Practical Engineering Concrete Series video called "Why SpaceX Cares About Concrete" at this link.
After you have watched these videos, consider the account of a recent Starship launch (3 March 2024) as described below.
______________________________________________________________________________
Sidebar: To put the nuances of heat effects on concrete and embedded reinforcing steel into perspective, we consulted ASTM publication STP 169-D chapter 25: "Resistance to Fire and High Temperatures", where we learned the following by contributing author Stephen S. Szoke:
- When heated, non-refractory, normal weight concrete (NWC) dehydrates between 400 °F and 800 °F. It is in this zone when the "development of distress and a change for the worse" can begin.
- "The length of time before the steel reaches a critical temperature is when the moment capacity is reduced to the applied moment. In a fire this depends on the amount of cover to the steel and on the insulation properties of the concrete. The influence of cover is striking. For the same normal weight concrete exposed in a standard fire test for 1 hour, steel with only 1-inch cover would reach over 800 °F whereas, with 2-inch cover, the steel temperature would be about 400 °F. With 3-inch cover, the steel would probably be hardly warm to the touch."
- Concrete-encased reinforcing steel bars will recover much of their lost strength when the bars cool and don't usually need to be replaced unless the bars are twisted or otherwise mechanically distorted.
- Jet engine exhaust can reach temperatures up to 1250 °F, 3500 °F at full afterburner; with a blast velocity of 3500 feet per second (fps).
- Although knowledge in the public domain is limited, rocket and missile engine exhaust temperatures may skyrocket to 5000 °F, with exhaust blast velocities up to 8000 fps.
See below for more about ASTM STP 169-D... the so-called ASTM "Blue Bible".
______________________________________________________________________________
Full Disclosure, front story: On 16 July 1969, this writer's eyes and ears were glued to an old RCA black-and-white, rabbit-eared antenna TV set. The occasion? Countdown sequence and liftoff of the Apollo 11 "moon shot". Some might say that the visual portion of the live feed from the launch site was the money shot. But for this nerdy 13-year-old, the sounds of the launch sequence and the following booster staging callouts by the voice of Mission Control were the game changers. In fact, one wonders if those witnesses who experienced the event only via radio may have gotten the better part of that deal.
Now...fast-forward to 3 March 2024, when the reusable SpaceX Falcon 9 "Crew Dragon" (as opposed to "Cargo Dragon") launched 3 NASA Crew-8 astronauts and one hitchhiking cosmonaut into low earth orbit (LEO) on the way to rendezvous with the International Space Station (ISS). No question--this was a magnificent night launch. Thanks to 55 years of technological advances, the sights-- and sounds--of the event could now be experienced using a hand-held device tuned to the social media platform called "X".
Once again, the voice of Mission Control and the entire audio feed from the launch site was sensational. (N.B. The launch audio-visual broadcast was committed to digital celluloid...you can hear the sounds plain as day with your own ears via the link to the official NASA broadcast given below. The NASA broadcast video length is a bit less than 5 hours. The segments described below kick in at elapsed video time stamp at about the 4:09:00 mark at the bottom of the frame. Also pay attention to the digital clock at the upper left-hand corner of the frame, or roughly T-minus 00:02:19).
At T-minus 00:01:45, the voice of Mission Control repeats the announcement that the loading of liquid oxygen (aka "LOX load") into booster stage 2 is complete.
At T-minus 00:01:29, gantry microphones are turned up, and we can hear the sound of gas venting from the Falcon 9 stack.
At T-minus 00:01:15, this announcement comes from the voice of Mission Control:
"Something else you might see here in a few moments is water being poured onto the pad...because rockets are super-loud, the sound can impart loads back on the rocket itself. So that water helps absorb and prevent the sound from hitting the structure and reverberating back on to the rocket".
___________________________________________________________________
Question: We are under subcontract to pump, place and finish (P-P-F) 12 floors of normal weight concrete (NWC) slab on metal deck (SOMD). Each floor is being placed in two pours measuring 21,000 square feet (SF) each. We have been averaging 726 cubic yards (CY) per floor, placed with a 36-meter pump and a crew of 11 masons and 6 laborers.
This mid-rise project was bid based on the P-P-F scope happening say late spring into mid-summer. Due to a change in Ownership, the schedule was delayed, causing the project schedule to push the start of our deckfill scope into late fall. As part of the schedule recovery plan, the Owner cut us a change order to cover Saturday placement costs (e.g. overtime for all labor and mobilization cost for the concrete batch plant to open on a weekend).
After 5 floors of same-kind work, our P-P-F crew settled into a nice, smooth rhythm. We outsmarted what little learning curve there was and went into cruise control from there.
We were in the middle of pour 2 on the 6th floor, about 150 CY in when KA-BOOM!!!! Our foreman called me and reported an unusually loud noise for a construction jobsite had just shaken everyone up. Evidently, the general contractor (GC) had come down with a serious case of the vapors when he heard about it and told us to start thinking about setting an emergency construction joint (aka bulkhead) until they could figure out what happened. We had to call in carpenters and send a few of our labor crew along with the GC's lone guy on site--plus the inspector--to search every floor for apparent signs of damage. We also had to call the batch plant and tell them to put a hold on the delivery.
Our foreman checked the top surface of the slab concrete placed earlier that day, and did not see anything unusual.
Just when our carpenters arrived on site, we got a call from the GC telling us this was all a false alarm. The structural engineer advised that the loud noise was simply the steel building "settling" at some of the bolted connections, and it was OK to complete the day's concrete placement.
The steel structure is founded on pile caps and grade beams. The piles extend down to bedrock. What kind of settlement could we possibly be talking about here?
Answer: From your description, it appears the phenomenon your P-P-F crew experienced that quiet Saturday morning was what the steel trade refers to as "banging bolts". To oversimplify enormously, it is pretty much what the structural engineer said: the structural steel frame of the building is settling down (as opposed to settling in elevation). When this happens, the noise-especially to someone unfamiliar with the usual loud jobsite sounds- can be quite startling.
Here at the ASCC Technical Division, we found a report in our vast archives of a 2015 case near Boston where the "bolt banging syndrome" at an elementary school caused the structure to be evacuated and shut down for a day.
There appears to be competing theories that explain the root cause of the noise. But most agree such raucousness is caused when the faying surfaces in a slip-critical bolted connection overcome friction and actually slip, converting a slip-critical bolted connection into a bearing connection when the weight of the tributary area forces the connection to slip--and slams the steel at the connection down onto the bolt. In other words, at some point the applied loads overwhelm the friction between the steel faying surfaces and "kaboom!"
The easiest way we found to get a grip on this is to view the first 3 minutes of a video presentation by Anthony Battistini, where the concepts of "slip-critical" and "bearing" bolted connections are clearly explained and demonstrated:
As concrete contractors, we routinely set embeds fitted with shear tabs in concrete walls and column sides to carry future follow-on bolted structural steel members. It may be helpful for us to gain an understanding of the steel trade's work...and the occasional sounds a new steel frame can make when you least expect them.
(N.B.: As ASCC Hotline callers know, if anyone wants to know about concrete building movement, all they need to do is visit a post-tensioned concrete structure during-- and just after--its construction.)
___________________________________________________________________
Question: About 14 months ago, we installed a raised concrete "aeration floor"--16 inches above the slab on ground--inside a 48-ft. diameter sheet metal grain storage bin. The 1810 SF concrete slab was placed over a proprietary corrugated metal deck and steel vertical support system. The 40-ft. tall grain bin enclosure is corrugated steel as well. Nominal concrete compressive strength was specified at 4000 psi. Out here in our market, such grain bin work is commonly accomplished with off-the-shelf, brand "X" ready mix concrete featuring a simple bull float final surface finish.
After about a year in service, there was a grain fire inside of the structure. Once the debris had been removed, the Owner asked us to perform a quick condition survey of the slab. The top slab surface was charred, to be sure, but otherwise (in our opinion) the slab looked just fine. An informal "Swiss hammer" rebound test was performed, and all indications were that the concrete appeared to have 4000 psi compressive strength--or better.
Nevertheless, the structural engineer is saying he recommends the slab be removed and replaced. The Owner and his insurance carrier have not yet decided on a course of action.
Does the ASCC Technical Division/Hotline have available any literature that discusses fire damage to a concrete slab? We have no skin in this game; but the Owner is a good, long-time customer, and in the name of excellent ASCC contractor customer service we want to provide backup that can support our belief that the existing slab is fit for purpose.
Answer: We are sending to you (under separate cover) some industry documents that discuss how to approach and assess fire damage to concrete. It appears the Owner and the insurance company are on the fence regarding the "remove and replace" option.
Because you were approached strictly as a "consultant" to weigh in as viewed through the lens of the concrete contractor of record, perhaps you might float an option that might just help convince all stakeholders to reconsider...and declare the existing slab fit-for-purpose.
Propose the Owner have 4 cores taken in the "worst" area of each quadrant of the slab. This would allow both visual examination and compressive strength testing to confirm the concrete strength in place is 4000 psi or better. Since you are likely to be the contractor of choice if the "remove and replace" option is used, you can easily estimate the costs involved and compare your number to the quote for testing the Owner solicits from his test lab. Might well be an investment worth making for all stakeholders.
One thing's for sure: if the remove and replace, "scorched earth" option is implemented, it should be a simple matter to sift through the wreckage and see with you own eyes the visual condition of the concrete. We can tell from your description of the ready mix that the possibility of fire damage inside a metal grain bin may not have been on the engineer's mind during design. In other words, the mix design used in the original construction did not include any "refractory" ingredients.
Either way, it's win-win for you.
________________________________________________________________
Question: We have a poured slab with a crooked spot in a sawcut joint as shown in the attached photograph. We are unable to find any documentation regarding the tolerances for sawcuts. Are you aware of anything regarding this issue?
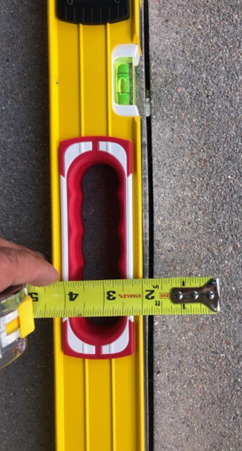
Answer: Let not your heart be troubled. The edge of the yellow level is set at the theoretical design plan center of the sawcut. It appears that the sawcut has wandered roughly a quarter inch to the right of perfection. If the concern is horizontal plan location of the as-built sawcut, you are home free. According to ACI 117-10 Specification for Tolerances for Concrete Construction and Materials section 4.2.1, the horizontal sawcut deviation is specified as plus/minus 3/4-inch. The ACI 117-10 commentary section R4.2.1 confirms this tolerance is "driven by aesthetic concerns", e.g. not a structural concern per se.
Should the depth of the sawcut become an issue, ACI 117-10 section 4.9.1 specifies the depth of the sawcut joint can deviate from nominal design depth with a tolerance of plus/minus 1/4 inch.
___________________________________________________________________
Insider's note: Here's another extremely high-value concrete industry reference book that ASCC members should consider adding to their library: "Significance of Tests and Properties of Concrete & Concrete-Making Materials". Published by the American Society for Testing and Materials International (ASTM), this 664-page manual is now available in both hard copy and searchable pdf (stock number STP 169-D). Here in the ASCC Technical Division, we refer to it as the "Blue Bible". If you visit this link, you can read the particulars, along with a free pdf file called "STP Individual Article Download" that provides the table of contents; titles of all 57 chapters, and authors of each chapter, including chapters written by concrete experts Ken Hover and Colin Lobo. Highly recommended.
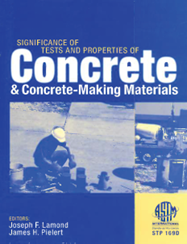
__________________________________________________________________
Question: We know flat slabs aren't perfectly level and some ponding should/could be expected. Are you aware of any code, standard or literature that discusses ponding water on a slab and what is an acceptable timeframe for evaporation of the water?
Answer: There is plenty of literature published by the ASCC Technical Division regarding birdbaths on concrete slabs. ASCC Position Statement #7: Birdbaths on Concrete Slabs tells us that--as you say--expectations of birdbath-free work are unrealistic. We are sending to you under separate cover a copy of a Concrete International article titled "Birdbaths: Expectations vs Reality" written by Bruce Suprenant, which explores the birdbath phenomenon in detail.
Perhaps the best technical explanation of the birdbath phenomenon--and why a birdbath-free slab surface is impossible to build--appears in the ASCC publication called "Tolerances for Cast-in-Place Buildings", a tour-de-force tolerance book authored by former ASCC Hotline Operators Bruce Suprenant and Ward Malisch.
Here's one of several birdbath examples from that ASCC tolerance book:
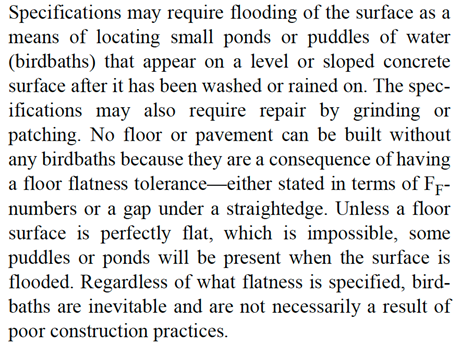
Unfortunately, we cannot find any mention of allowable expected water evaporation time in ASCC, ACI, or other concrete trade publications.
But sometimes we can venture out of our concrete world and see what's in the other guy's playbook. In this case, we find what we are looking for-- published by our colleagues in the residential home building business. According to the National Association of Homebuilders (NAHB) publication titled "Residential Construction Performance Guidelines: Consumer Reference, Fifth Edition", the issue of birdbath water evaporation time appears in several sections related to residential concrete (and some asphalt) work as follows:
For Driveways and Sidewalks, the NAHB Performance Guideline in section 12-4-2 for asphalt pavement states "Standing water greater than 3/8 inch in depth should not remain on the surface 24 hours after a rain".
For Driveways and Sidewalks, the NAHB Performance Guideline in section 12-4-7 states "Standing water that is 3/8 inch deep on a sidewalk 24 hours after the end of a rain is considered excessive".
For Concrete Stoops and Steps, the NAHB Performance Guideline in section 12-2-2 states "Minor amounts of water can be expected to remain on stoops and steps for up to 24 hours after rain".
(N.B.: If you really want to know the truth about it all, the wording in sections 12-4-2 and 12-4-7 seem borderline questionable. But hey--at present--that's the best we can find in print for rainwater. On the other hand, bleed water evaporation time is an unrelated--but currently popular--topic of interest when the discussion turns to initial curing of concrete slabs).
___________________________________________________________________
Question: We are building a concrete parking structure that features two floors below street level. Once the sheeting and shoring was completed, the first order of business for us was to place a 3-inch-thick mud slab over some 40,000 square feet (SF) of real estate. We placed the mud slab in one mobilization on a Friday in 30° F weather. The next concrete placement on the schedule was for a 4-ft. thick foundation mat slab.
We brought a 3-man layout crew in on Saturday to establish control lines on the newly placed mud slab and then lay out the concrete outlines for every wall and column. We use blue chalk line and bright orange spray paint to preserve the lines and to make them easy to see when standing on the top mat reinforcing steel, or when dropping a plumb bob down 4 feet to transfer up the outlines for wall and column rebar templates to be attached to the top layer of steel.
(As any veteran ASCC concrete contractor can tell you, spending a little overtime for the layout crew on a Saturday helps reduce the grief factor first thing Monday morning when the rebar guys start flying 60-ft. long bundles of #11 bars into the hole is money well-spent.)
The ambient temperature on Saturday morning was still below 30° F, so we decided to fly an empty 50-gallon trash drum down into the hole to use as a fire barrel. We looked down in the hole, and could see some random people down there who were gathered around a good-sized fire on the mud slab. The problem we had was how to evict these uninvited jobsite visitors. One of our crew hollered to them and asked them to leave, but they ignored the request. We were just about ready to call the police when our superintendent showed up. He told us not to do anything--these folks would soon be gone.
The three of us went out and hollered some more, and the visitors took the hint and left the site...without putting out the campfire. A few minutes later, we watched and listened as the mud slab concrete under the campfire exploded, sending debris everywhere.
We have told this story to several people in our main office, but no one believes it was the concrete that exploded. On the jobsite, anyone could see plain as day where the mud slab needed to be replaced. Does the ASCC Technical Division have any information about exploding concrete?
Answer: Under the right conditions, concrete can indeed explode. The phenomenon is defined as "explosive spalling" as reported in ACI 547R-79(97) Refractory Concrete: Abstract State-of-the-Art Report as follows:
"EXPLOSIVE SPALLING- A sudden spalling which occurs as the result of a build-up of steam pressure caused by too rapid heating on first firing."
Further explanation is offered in section 6.4 Drying as follows: "The large amount of free water in the refractory concrete necessitates a drying period before exposure to elevated temperatures. Otherwise, the formation of steam may lead to explosive spalling during firing."
There are a raft of videos and news reports that feature cases where highway pavements in Missouri and Louisiana, for example, exploded due to elevated daytime pressure that built up inside the roadway slabs. Those can be found by simple internet search.
If you want a scientific laboratory research example, there is a short, roughly 1-minute video titled "Concrete Can't Burn, But it Can Blow Up", produced by the LiveScience channel.
___________________________________________________________________
(N.B.: Any and all references--however oblique--to work product by Gibbons, Hill, Beard and Robert Weston Smith in the above are purely intentional. If you know...you know. References available upon request for most anything you see reported above.)
___________________________________________________________________