Jim Klinger, Concrete Construction Specialist
The Voice Newsletter February 2024
The Use of Laser Scanners
Full Disclosure: Imagine, if you will, the following scenario. You are an experienced project manager, patiently waiting to collect your retention for the reinforced structural concrete portion of a large, wood-framed condominium project. The stick framing begins at grade level--there are no basement or subterranean parking levels. The reinforced concrete slabs on grade are your standard brand "X" variety: 6 inches thick, 4000 psi at 28 days. Mid-depth reinforcement is #4 bars at 16 inches on center, each way (OCEW), supported on precast dobies on 15-mil vapor barrier over a well-prepared subgrade. Each slab on grade features a 9000 square foot (SF) footprint, 45 feet wide and 200 feet long, with sawcut control joints spaced at 15-foot centers in both directions. There are no reinforced concrete columns or masonry walls, but sill plate anchor bolts and seismic hold-downs for the vertical wood framing abound.
Your subcontract scope included 15 each of the 9000 SF slabs on grade. Looking back over the job, you did everything by the book. The schedule and concrete placement logistics for each of the 167 neat cubic yard (CY) pours were carefully choreographed, thanks to close collaboration with the general contractor (GC), the ready-mix supplier, and the City. During the preconstruction meeting, all parties discussed the specified floor flatness requirements-- and agreed on the means and methods the Owner's inspection agency would employ to determine contract compliance. Your finishing crews had no problem meeting the specified overall floor flatness and levelness callouts of FF 35/FL 25. Each and every test report indicated all flatness and levelness testing was completed and reported within the allowable 72-hour window, and your work product passed with flying colors. No overtime was needed for your finishing or labor crews, and your overall job cost is looking good. There were a minimal amount of punch list items, all completed and signed off 6 months ago. Due to pandemic-related supply chain problems, the wood framing subcontractor is just now mobilizing on the jobsite. Almost all of the follow-on trades have been delayed as well. But your work is long since complete-- all you are doing now is waiting for your retention payment.
And then the unthinkable happens. You get that email...or that phone call...from the GC. The follow-on flooring subcontractor has commissioned an as-built survey of your slab surfaces, conducted with a laser scanner last week. The GC transmits a multi-colored survey plan--a so-called "heat map"--to you, along with notice that your retention payment is now on hold. In essence, the GC tells you "Here's the heat map that shows your work is in the wrong place, and now you owe me cash".
Or "now you owe me grinding."
Or "now you owe me leveling compound".
The GC typically ends such notices with "The project has already been delayed, you need to get your repair crew out there now to commence fixing the floors. And don't forget to submit your recovery schedule".
Sometime during 2017, the ASCC Hotline began fielding phone calls from contractor members who had been to the movie described above. In fact, they had front-row seats. ASCC members were being presented with heat map plans and told their work was not in compliance with the construction documents and backcharges were being prepared.
The ASCC Technical Division disagreed.
Since there was no published guidance in the industry literature that described the use of laser scanners to determine top of concrete slab contract F-number compliance, ASCC designed a study to test and report the tolerance-measuring performance of 8 laser scanners to Joint ACI-ASCC Committee 117 Tolerances. The ASCC study and its results were presented in the ACI Concrete International January 2019 and February 2020 issues. Were the GC's justified in backcharging ASCC contractors based on laser scanner heat maps?
In a nutshell, the results of the 2018 ASCC study showed that we were unable to recommend the use of laser scanners to determine contract F-number tolerance compliance. In other words, we believed that laser scanning technology--while quite useful in other concrete construction applications-- was not ready for prime time for contract F-number tolerance compliance purposes.
By-products of the ASCC study included two very successful Laser Scanning Workshops held at the World of Concrete, formation of ACI 117 Subcommittee 117-L Laser Scanning and drafting of a new ACI-ASCC tolerance document (still in progress) with the working title "Guide to the Use of Laser Scanning for Concrete Tolerances".
Fast-forward now to 2024. Laser scanner technology continues to evolve, and the use of these instruments is becoming commonplace among ASCC contractors for various applications. We still believe reliable laser scanner use for F-numbers is out on the horizon. But has the technology progressed to the point where the laser scanners can be used to reliably evaluate other ACI 117 tolerances e.g. tolerances for plumb, elevation and location?
Part of the answer lies in the September 2023 ACI Concrete International article titled "Laser Scanning Basics for Concrete Tolerance Verification", co-authored by ASCC member Conco's Leo Zhang (Chair of ACI Committee 117-L) and the U.S. Institute of Building Documentation's (USIBD) John Russo. Currently, concrete contractors are using laser scan technology in planning and preconstruction phases to evaluate staging, safety and truck routing. Laser scanners are effective in quickly assembling volume calculations for mat pours and for determining extra perimeter wall concrete needed when below-ground shoring is misplaced. The laser scanners are also being used in certain Quality Assurance/Quality Control (QA/QC) applications as well as Building Information Modeling (BIM) deliverables. But according to Zhang and Russo, there is still testing that needs to be done.
To that end, Zhang has recently issued a two-page "Call for Participants: A Laser Scanning Interlaboratory Study on Selected ACI 117 Tolerance Compliance Verification".
The proposed testing would be similar to the original 2018 ASCC study conducted in Walnut Creek, California. Testing would take place on a San Francisco Bay Area construction jobsite on a Saturday and Sunday in July 2024, actual weekend dates TBD. Both vertical and horizontal concrete elements would be tested. Ten participants are envisioned to take part representing different U.S geographic regions. In addition to data collection, results of the July 2024 study will be submitted for a future ACI Concrete International presenting a compilation of best practices learned from the study.
For more information, contact Leo Zhang, 925-348-5309, lzhang@conconow.com.
ASCC 3-D Laser Scanning Study, Part 1, Concrete International January 2019 and Part 2, Concrete International February 2020
Laser Scanning Basics for Concrete Tolerance Verification, Concrete International September 2023
____________________________________________________________________________________________
The Lombardi Rule
Question: I attended a safety meeting held last spring at one of our jobsite trailers. Before our meeting convened, I caught part of a speakerphone conversation among our field superintendent, our carpenter foreman, and the ASCC Hotline. The discussion I overheard was related to the quality of architectural concrete wall surface finishes. It sounded like the architect showed up to our jobsite with a magnifying glass to review the latest lift of shear walls; poured a week prior and stripped 2 days after concrete placement. I kept hearing the term "Lombardi Rule" used by the Hotline operator, but unfortunately was unable to hear the balance of the conversation. Evidently, the dispute with the architect was settled and I have been too distracted follow up until now. What exactly is the "Lombardi Rule", and how can such a rule be used by ASCC members?
Answer: The so-called "Lombardi Rule" is an informal shorthand term coined by a Hotline operator here in the ASCC Technical Division. The term is used when referring to the "final acceptance of architectural concrete" determination procedure stated in ACI 301-20: Specifications for Concrete Construction.
According to ACI 301-20, section 6.3.12 specifies the following procedure: "Upon completion of architectural concrete, including surface repairs and patching of tie holes, final acceptance is based on matching the architectural cast-in place concrete with accepted field mockup when viewed at 20 ft in daylight."
The "Lombardi" part is a sentimental old-school tribute to Vince Lombardi (1913-1970), legendary National Football League (NFL) coach and author of "Run to Daylight".
The Lombardi Rule should be invoked by a concrete contractor when the reviewer of an architectural concrete surface stands a few feet away from the work and then pronounces the work unacceptable based on "defects" (e.g. bugholes, etc.) as seen--and then subjectively judged--from only a few feet away.
A more detailed explanation of the Lombardi Rule can be found in ACI 347.3R-13 Guide to Formed Concrete Surfaces, which explains that "when evaluating exposed concrete surfaces, the overall impression viewed from an appropriate viewing distance is the main method of evaluation". But what constitutes an appropriate viewing distance?
ACI 347.3R-13 section 7.2 provides the answer as follows:
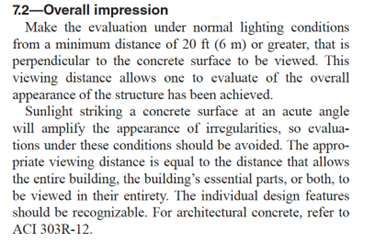
It should be noted here that the application of the Lombardi Rule should be discussed at every preconstruction conference where architectural concrete is part of the scope of work. In some cases, construction documents may call for a viewing distance less than 20 feet. ASCC members who specialize in tilt-up work, for example, should be mindful that ACI 301 section 12.3.9(a)(d) specifies a viewing distance of only 10 feet for evaluation of tilt-up panels that require a Smooth Panel Finish 3 (SPF-3).